Data and Knowledge Gaps of a Water Bottling Facility Inventory and Select Water-Use Dataset, United States
Links
- Document: Report (4.01 MB pdf) , HTML , XML
- Data Releases:
- USGS data release - Inventory of water bottling facilities in the United States, 2023, and select water-use data, 1955–2022
- USGS data release - Inventory of water bottling facilities in the United States, 2024, and select water-use data, 1955–2023 (version 2)
- Download citation as: RIS | Dublin Core
Acknowledgments
The U.S. Geological Survey (USGS) Water Availability and Use Science Program funded this work. Assistance locating facilities for the inventory was provided during the first year of the project from USGS colleagues in the following water science centers: California, Colorado, Caribbean-Florida, Iowa, New England, Ohio-Kentucky-Indiana, Oklahoma-Texas, Oregon, Pennsylvania, South Atlantic, Upper Midwest, and Virginia-West Virginia.
Abstract
In 2023, the U.S. Geological Survey developed a national inventory of water bottling facilities for the United States, including information about locations, water sources, water use, and a collection of other attributes. The purpose of the inventory was to provide information about water bottling facilities needed to assess and improve understanding of local-, regional-, and national-scale hydrologic and socioeconomic effects resulting from water extraction for bottling. Beverage types coded in the North American Industry Classification System under subsector 312 (Beverage and Tobacco Product Manufacturing) were compiled; however, facility information was often not publicly available, time intensive to search manually, and difficult to verify because there are no nationally available facility lists. A separate evaluation of facilities in the Great Lakes region identified some facilities that were missing and some with incorrect information. Ancillary facility attributes were primarily available from a proprietary business dataset and water-use data could only be acquired for a small subset of facilities. These limitations and deficiencies may affect the types of analyses that can be done using the inventory information. Therefore, the following data-quality aspects are used to describe the information compiled in the facility and water-use tables: completeness, uniqueness, validity, timeliness, accuracy, consistency, and accessibility. The resulting implications of the data and knowledge gaps are that users of the data may need to make additional evaluations of the inventory information for some analyses.
Introduction
The consumption of bottled water has grown steadily in the United States; in 2022, it was the number one beverage sold in the United States by volume for the seventh year in a row (Beverage Marketing Corporation, 2023). However, the hydrologic and socioeconomic effects of water extraction for bottling have not been systematically assessed, and certainly not at a national scale. There is no comprehensive national inventory of water bottling facilities that includes the volume of water extracted and associated water source, which are needed to begin to assess effects of extraction of water for bottling. The U.S. Geological Survey (USGS) developed an inventory of water bottling facilities, including information about locations, water sources, water use, and a collection of other attributes (Buchwald and others, 2023) to use as a basis for developing a strategic approach for selecting areas within the United States where directed research and assessment would improve understanding of local-, regional-, and national-scale hydrologic and socioeconomic effects of water extraction for bottling.
The inventory of facilities that bottled water or other beverages containing water (including soft drinks, beer, wine, or spirits) or that manufactured ice was compiled by combining available datasets from multiple sources (Buchwald and others, 2023). The inventory included (1) self-supplied water bottling facilities that operated their own water-supply infrastructure and obtained water from their own water sources, including wells, springs, and surface waters; (2) publicly supplied water bottling facilities; and (3) water bottling facilities with diversified water supplies in that they obtained water from their own sources and received water from a public-supply system. Facility classifications were based on the North American Industrial Classification System (NAICS) code (NAICS Association, 2023). The NAICS is the standard used by Federal statistical agencies in classifying business establishments for the purpose of collecting, analyzing, and publishing statistical data related to the U.S. business economy. The NAICS is organized into a hierarchical structure with 3-digit codes representing the subsector and 6-digit codes representing the national industry and was used to select industry types to include in the inventory. Beverage types in subsector 312 (Beverage and Tobacco Product Manufacturing) were compiled for this effort and included facilities with the following NAICS codes as a primary or secondary classification type: (1) 312111, soft drink manufacturing; (2) 312112, bottled water manufacturing; (3) 312113, ice manufacturing; (4) 312120, breweries; (5) 312130, wineries; and (6) 312140, distilleries.
The inventory included information for 43,365 facilities in all 50 States, Washington D.C., and three territories (Guam [not shown], Puerto Rico, and Virgin Islands) and water-use data for 257 facilities in 34 States. Compilation of this national inventory of water-bottling facilities relied on reviewing and merging data from multiple sources of information, such as state agency and business databases. This process had limitations owing to varied data qualities, incomplete attributes, and the time required to verify information, which created potential issues that users of the data need to be aware of. Therefore, the data and knowledge gaps described in this report may have potential implications for the utility of the facility and water-use information available from Buchwald and others (2023). Further review of the inventory identified some areas where improvements could be made including addition of facility attributes for facilities with water-use data, removal of inaccurate facilities, identification of potential duplicate facility listings, and addition of missing facilities. For example, a separate review of facilities in the Great Lakes Region identified missing facilities, incorrectly classified or located facilities, and duplicates. Many of these updates have been made in a version 2 of the inventory, which is published and available in Buchwald and others (2024).
Purpose and Scope
This report describes data-quality aspects of the inventory of water bottling facilities and water-use information (Buchwald and others, 2023). Facilities were included based on NAICS codes. The inventory included facilities in the beverage industry manufacturing groups in subsector 312, which are defined as follows:
-
(1) 312111: Soft drink manufacturing (establishments primarily engaged in manufacturing soft drinks and artificially carbonated waters);
-
(2) 312112: bottled water manufacturing (establishments engaged primarily in purifying and bottling water, including naturally carbonated);
-
(3) 312113: ice manufacturing (establishments primarily engaged in manufacturing ice);
-
(4) 312120: breweries (establishments primarily engaged in brewing beer, ale, lager, malt liquors, and nonalcoholic beer);
-
(5) 312130: wineries (establishments primarily engaged in one or more of the following: growing grapes and manufacturing wines and brandies, manufacturing wines and brandies from grapes and other fruits grown elsewhere, and blending wines and brandies); and
-
(6) 312140: distilleries (establishments primarily engaged in one or more of the following: distilling potable liquor [except brandies], distilling and blending liquors, and blending and mixing liquors and other ingredients).
Other beverage classifications in subsector 311 (Food Manufacturing), such as juice, coffee, and tea, may also incorporate water into a final product but were outside the scope of this effort because these industry groups focus primarily on food products rather than beverages. These facilities were generally not included unless the facility had multiple product lines and was also classified within subsector 312. These other beverage types may be included in some cases, though, owing to an incorrectly reported classification leading to unavoidable uncertainties in the dataset. For example, some facilities were included with a primary NAICS code of something other than 312 because the business had a secondary product line classified within the 312 group. “Water bottling facilities” refers to all these beverage bottling or ice manufacturing facilities, and hereafter, will be referred to as “beverage bottling facilities” in this report. Some parts of the report focus only on facilities that provide drinking water packaged generally in plastic or glass bottles to consumers, and these facilities will be referred to as “bottled water facilities” in this report.
When using these facility and water-use information and data in further analyses, users should consider the reliability and limitations of the inventory, potential uncertainties in the facility information, and additional considerations for other studies. Seven data-quality aspects are used to describe potential data issues and limitations. This report identifies data and knowledge gaps of the inventory and water-use tables and the potential implications of these data and knowledge gaps. This report also describes some updates to Buchwald and others (2023) (version 1 of the inventory of water bottling facilities), which are available in Buchwald and others (2024) (version 2 of the inventory).
Analysis of Facility and Water-Use Information
Beverage bottling and ice manufacturing facilities were compiled from multiple sources of information to create the inventory. Facility attributes, such as location, bottling type, source of water, other facility characteristics, and water-use quantities were included where available (table 1). These facility characteristics provide information for comparisons between facilities and could help with estimation of water use where those data were unavailable. Process steps for compilation, data review, attribute assignment, and quality-control analyses are described in the inventory (Buchwald and others, 2023).
Table 1.
Beverage bottling facility inventory column names and descriptions (data from Buchwald and others, 2023).Data-review and quality-assurance checks were completed during all phases of the creation of the inventory. This report describes data quality of the inventory and identifies issues and potential deficiencies that could limit the usefulness of the dataset. To quantify data quality and the potential implications, the following seven aspects were used: (1) completeness, (2) uniqueness, (3) validity, (4) timeliness, (5) accuracy, (6) consistency, and (7) accessibility. Completeness provides a measure of the amount of missing data and refers to the extent to which a dataset has all the relevant and necessary information for its intended purpose. Uniqueness provides a measure of the potential for duplication of information. Validity provides a measure of how well the data conform to formatting standards, such as common units of measure. Timeliness provides a measure of how current the data are. Accuracy provides a measure of the degree to which the data represent the characteristics of the real world. Consistency provides a measure of how well the datasets and data values compare to each other. And finally, accessibility provides a measure of how useable and understandable the data are and how accessible and easily discoverable data sources were for finding information. Each of these data-quality aspects can be applied in multiple ways as descriptors of the information published in the inventory, in reference to the multiple information sources, and (or) in the effort required to construct the inventory.
Subsequent sections describe the data-quality aspects of the facility inventory and water-use information and the potential implications of data and knowledge limitations, inconsistencies, and incompleteness. Data aspects are illustrated through graphs, charts, tables, and maps. Some charts are organized so that similar facility information, such as location, data source, or facility characteristics, are grouped together rather than in order of appearance in the inventory table.
Discussion of Data-Quality Aspects
The condition of the facility and water-use information published in the inventory is described using seven aspects of data quality. The information provided in the inventory might be appropriate for some analyses and not others owing to how and what information was compiled. Data issues and knowledge gaps might limit the kinds of analyses that can be done with a given set of information. Therefore, these descriptions of data quality and limitations help to ensure that the beverage bottling facility inventory and associated data (Buchwald and others, 2023) are used appropriately.
Background
In response to legislation enacted by the U.S. Congress in 2021 and 2022 (U.S. Congress, 2021, 2022), the USGS compiled a comprehensive national inventory during 2021–23 that included 43,365 beverage bottling facilities that add water in the production of soft drinks, bottled water, ice, beer, wine, and liquor located in 54 States, territories, and districts (Buchwald and others, 2023) (table 2, fig. 1A). Of the 27 facilities with a primary value NAICS code of −9999, indicating a primary business operation not within the 312 subsector, 26 had a secondary NAICS code of Bottled Water and 1 had a code of Distilleries.
Table 2.
Total number of facilities by beverage bottling type (data from Buchwald and others, 2023).States with the largest number of inventoried beverage bottling facilities included California with 9,392 facilities; Florida with 3,054 facilities; and Texas with 2,707 facilities. As of 2023, the facility inventory (Buchwald and others, 2023) included 10,192 facilities that produce bottled water as the primary product or as a secondary product line where the primary product line is something other than subsector 312. States with the largest number of bottled water facilities that were inventoried included California with 2,327 facilities; Texas with 997 facilities; Florida with 852 facilities; New York with 423 facilities; and Pennsylvania with 337 facilities (fig. 1B).
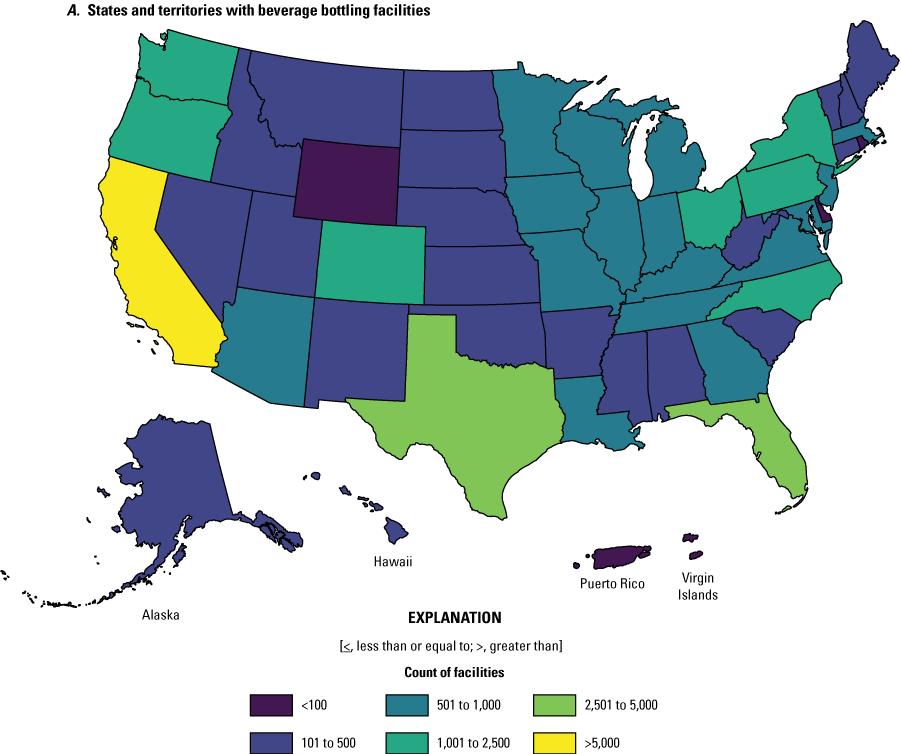
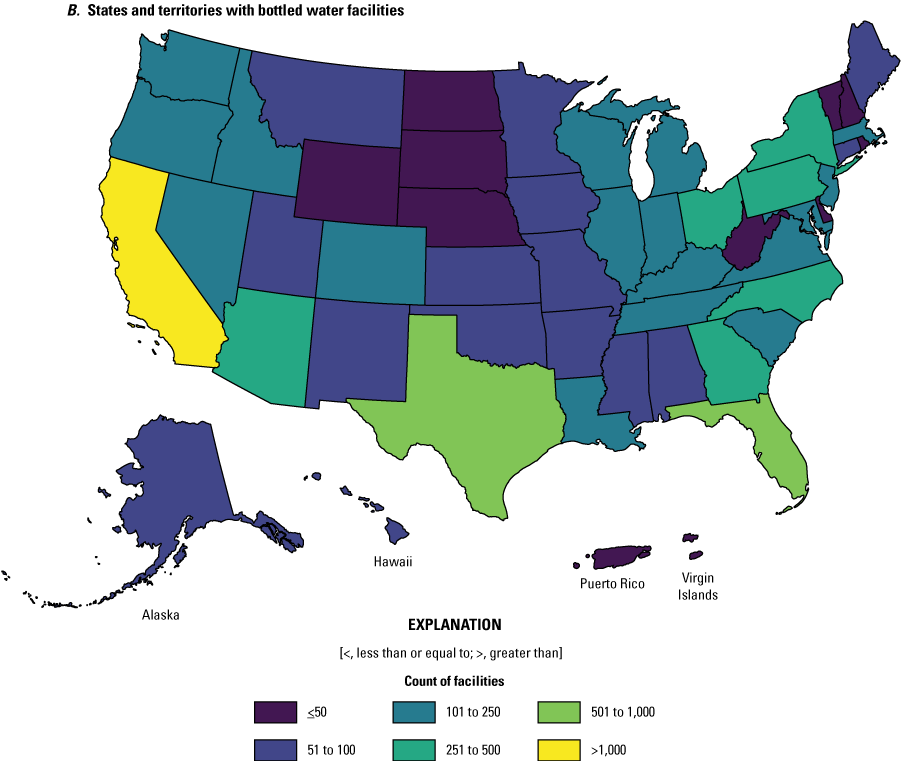
Number of bottling facilities in the United States in 2023. A, States with beverage bottling facilities. B, States with bottled water facilities (Buchwald and others, 2023).
Much effort was expended during the inventory compilation process to address as many data issues as possible; however, resolution of these issues proved to be very labor and time intensive. In a selection of more than 5,600 rejected records, the primary reason (40 percent) for excluding a facility from the inventory was due to a business type being incorrectly classified within subsector 312. About 20 percent of facilities were excluded owing to duplication among sources and another 20 percent were excluded owing to insufficient available information to confirm the facility location and status. The effort to create this inventory was challenging and the potential implications of these challenges are described in this report.
Facility Information
Information about facility locations and characteristics were needed to assess potential hydrologic effects of extracting water for beverage bottling operations. Facility information including bottling type, location, source of water, and other facility attributes were included in the facility table (Buchwald and others, 2023) (table 1). This section describes the data-quality aspects of the facility data and the potential implications of data and knowledge gaps.
Completeness
Facility data completeness was measured by the number of facilities in the inventory and accompanying facility location, type, and other attributes. Completeness included whether the data represent facilities spatially across the United States. Finally, completeness also included how well the ancillary data represent characteristics at each facility and the extent to which the dataset contains all expected and required information for a given purpose. Completeness included whether all beverage bottling facilities were accounted for and whether each facility had all attributes. Causes of missing facilities might be the result of (1) data not collected and provided by the data source, (2) unwillingness to provide information, (3) proprietary or disclosure restrictions, (4) limited knowledge of resources, (5) accessibility challenges, (6) user entry errors, or (7) time and cost limitations. The following sections describe facility, attribute, and water source completeness.
Facility Completeness
The project team strived to use the best available information for each region when compiling the facilities, such as finding relevant State agency programs or large company sites for manufacturing lists. A table titled “WBinventory_DataSources.txt” in Buchwald and others (2023) identifies data sources that were acquired. Bottling facility information was acquired from 79 sources, which included 69 State agencies (87 percent), 3 Federal agencies (4 percent), and 7 other sources (9 percent). In terms of completeness, none of the sources of information contained a listing of all beverage facility types across the United States. Within States, different agencies are often responsible for beverage facility tracking and permitting and for water-use reporting. Other potential sources of information are proprietary lists maintained by industry groups unavailable to nonmembers or require multiple purchases to access, thus limiting data accessibility and reproducibility. Furthermore, some sources of information have data-use restrictions limiting the release of site-specific information. Of these sources, almost 94 percent of facilities were identified through a purchase from Data Axle (2023). State agencies provided about 2 percent of facilities in the inventory, and the rest of the facilities in the inventory were from other sources, such as websites. Because the lists were from different sources and often had insufficient accompanying metadata, much effort was required to check the validity of all information to ensure data formats were comparable and to fill in information across multiple sources. This inventory is likely not a complete inventory of all beverage bottling facilities in the United States classified under NAICS code 312, because not all possible data sources could be discovered, facility numbers are constantly changing over time, and no source contained a comprehensive list of all current facilities.
Limited reviews consisted of key word searches, such as “dairy” or “coffee,” to remove facilities that should be classified under a different NAICS group than those intended for this inventory. Facilities, such as bulk water haulers for pool filling, laboratory water suppliers, and most water refill stations that are co-located within grocery stores and stand-alone water and ice service huts were largely not included in the inventory. Approximately 16,500 water-refill stations alone were identified nationally from two major water purveyors, WaterMill (WaterMill Express, 2021) and Primo (Primo water, 2021). A decision was made early in the project to exclude grocery store water-refill stations and chain retail store water and ice service huts from the final inventory because they are mostly on public supply. Additionally, it would be difficult to obtain customer sales data to make viable water-use estimates, and there would be no way to separate the water used for water bottling from the total water used by the grocery store. However, most water retail stores were left in the inventory (Buchwald and others, 2023) because they bottled water on-demand at an autonomous storefront location with typically a unique name making it harder to identify. Some patterns to facility names were noted, which included Pure Water, Water & Ice, Water Mart, Water Tree, and Water Store; however, even with these name patterns it was often difficult to differentiate a storefront location from a major beverage bottling production plant. Many facility names can be identified in the inventory as small businesses that employ 1–4 people, which could help with this effort; however, employment attribute information is not available for all facilities.
It is difficult to quantify the completeness of the inventory because this dataset is the first national comprehensive list. Omission errors (errors of exclusion) and commission error (errors of inclusion) can cause under- or over-facility representation. NAICS coding errors, duplicate businesses, and missing businesses were often determined during review of facility data sources. Within each NAICS grouping, the facility listing may be incomplete, especially for wineries (NAICS 312130); however, some NAICS groupings would be more complete than others.
The number of bottling facilities inventoried in Buchwald and others (2023) generally exceed those reported in other sources of information (table 3). The facilities compiled in Buchwald and others (2023) were often small businesses with fewer than 10 employees, which explains the higher counts. Facility counts for businesses with 10 or more employees in the inventory are similar to counts reported in the other data sources. Exceptions include soft drink manufacturing with 1,696 inventoried bottling facilities versus 3,046 “U.S. business entities” reported by the NAICS Association, though these business entities may include facilities for business operations other than bottling production, such as warehousing, distribution, and administration. Establishments included in the U.S. Census Bureau, County Business Patterns totals may be missed because (1) a multi-unit company structure is not created in the Business Register for very small employers (less than 10 employees), (2) the Report of Organization annual mail survey excludes companies with less than 500 employees unless administrative records indicate organizational changes adding or dropping establishments, and (or) (3) a company does not respond to the Economic Census or the Report of Organization. Also, the inventoried wineries (7,071) were likely an undercount because tracking this category was a lower priority than the other categories owing to resource limitations. The number of wineries reported in the business media and literature for the inventory period 2021–23 ranged from 4,284 (U.S. Census Bureau, 2021) to 16,397 for 2021 (VinePair, Inc., 2023). Employment data were obtained for 8,978 (88 percent) of the 10,192 inventoried facilities that produce bottled water as the primary or secondary product line; therefore, some counts may not be representative owing to the absence of employment information for comparison with other sources (Buchwald and others, 2023). An additional 51 bottled water facilities have been identified to have employment data added in version 2 of the inventory (Buchwald and others, 2024).
Table 3.
Comparisons of the numbers of inventoried United States beverage bottling facilities and beverage bottling operations compiled by other selected organizations.[NAICS, North American Industrial Classification System; --, not applicable]
Version 1: Buchwald and others (2023).
Facility counts with 10 or more employees is incomplete due to employment data not being available for all facilities in the inventory.
Version 2: Buchwald and others (2024).
Source: IBISWorld, Inc. (2021).
Source: NAICS Association (2023).
Source: U.S. Census Bureau (2021).
Source: Dun & Bradstreet (2023).
Source: VinePair, Inc. (2023).
The number of inventoried bottled water facilities having employment data and with 10 or more employees (786) was comparable to the number of bottled water production facilities (708) reported in 2021 by IBISWorld (IBISWorld, Inc., 2021). The NAICS Association (2023) reported there were 449 bottled water manufacturing and 16,906 beverage manufacturing “U.S. business entities” in 2023.
Attribute Completeness
Ancillary attributes were added, when available, to describe facility characteristics providing information about facility size, employment, sales, and year established (table 1). Ancillary attributes allow for comparisons between similar facilities and determinations of relative size and expected operations. The multiple sources consulted for lists of bottling facilities rarely contained complete facility information and relevant attributes (table 4). Some source datasets were missing locational coordinates or NAICS codes listing product types, thus requiring additional and often manual searches and identification of these data through other means. Some missing or inconsistent information could have resulted from data-entry errors in the source database or information being unreported by the facility. The ancillary data were limited primarily to records from a single purchased data source. Additional attributes might be identified from other proprietary business datasets if the facility were to exist in that source (for example, Dun & Bradstreet, 2024; Mergent, 2024). Some facility status information was discovered during review of online or State agency provided lists, such as when a facility began operations or when production of a product ceased at a business location, but the status was not checked for all business records owing to time constraints and data availability. In addition, other ancillary attributes not obtained may be helpful with determining potential hydrologic effects or describing relevant drivers affecting beverage bottling production. For example, sales data with multiyear records could be useful to determine potential effects over time.
Table 4.
Percent missing values for facility attributes.[Version 1 data from Buchwald and others, 2023; version 2 data from Buchwald and others, 2024; WB_TYPE, type of beverage bottling facility; YEAR_END, the year the facility closed, or production of a beverage product ended; YEAR_ESTBL, the year the facility was established; EMPL_COUNT, count of employees for the facility; EMPL_RANGE, range of number of employees for the facility; SALES_YR_AMT, reported dollar amount of sales for the facility; SALES_RANGE, reported range of annual sales, in millions of dollars, for the facility; FAC_SIZE, reported size range, in square feet, for the facility; FLEET_SIZE, reported fleet size range for the facility]
Water Source Completeness
Most facilities (42,268 or 97 percent) did not have water source information captured by data discovery. For these facilities, water sources were estimated using proximity to public-supply water service areas (Buchwald and others, 2022) or to other sources such as groundwater wells, springs, and surface-water bodies. Facilities located within a service area were estimated to receive water from the public-supply system, and facilities surrounded by other sources of supply were estimated to use that source of water. Facilities with spring water in the name were estimated to rely on springs, but the facility may have other sources as well.
Potential implications.—Incomplete data can compromise the validity and reliability of the data. Errors in facility counts could result in over- or underestimating the potential for hydrologic effects on water resources. In the absence of a complete list of beverage bottling facilities, the comprehensiveness of this list cannot be adequately determined. Wineries are likely undercounted, but the other categories are unknown. Therefore, additional work may be needed in local areas of interest to assess potential bottling facility locations. In addition, facility counts are constantly changing as facilities open, close, or transfer ownership, making accurate facility counts difficult to obtain. Collection of additional attributes could also be beneficial for a better understanding of facility characteristics and a representation of the potential for hydrologic effects. Attributes currently (2023) in the inventory are incomplete and are mostly insufficient to distinguish between major beverage bottling production and small store front refill facilities. These determinations can be attempted using attributes, such as employment and facility size or by searches using facility names, but manual investigation of individual facilities may be necessary to accomplish this distinction.
Uniqueness
Facility data uniqueness was measured by the degree of duplication among facilities. Each data source had some unique facilities, as well as duplicates within and between data sources. Beverage bottling facilities often change names, change ownership, merge businesses, or change business types over time, resulting in the same facility duplicated within the source dataset. More than one facility often appeared to be located at the same place, requiring investigation to determine whether it was the result of a name misspelling, facility opening/closing, incorrect facility location, or multiple businesses sharing one location. Name variations and imprecise locations made determination of potential duplicates problematic and time consuming. Therefore, counts of major water bottling brands were difficult to summarize unless production plants were listed on facility websites.
One measure of the similarity between facility names is use of the Jaro–Winkler method (Rdocumentation, 2023), which was used to assess facilities in each State to determine the potential for duplicate facility listings. Facility names combined with the county name and facility identification number were compared with every other facility-county-identification name combination within the same State and one Jaro–Winkler score calculated for each pair. Facility matched pairs with values close to 1 are very similar and pairs with values close to 0 are dissimilar. The match with the highest score among all matches for each facility was selected and compared to a threshold value of 0.9 to assess potential duplication among facilities within each State. In some cases, there were tied scores where a facility matched with more than one facility in the inventory. For determining counts of potential duplicates only one of the facility matches was counted; however, for evaluations of duplicate facilities each of these would need to be evaluated. Among U.S. States and territories, the potential for duplicated facilities ranged from 0 to 16.4 percent and equaled 7.3 percent overall with a total of 3,153 facilities that could be assessed further by location mapping, address matching, or web searches. An additional evaluation was done to determine the prevalence of duplicates for bottled water facilities. Overall, 1,001 (9.8 percent) potential duplicates were identified from 10,192 bottled water facilities.
Potential implications.—Duplicate facility listings within the inventory could bias the number of beverage bottling operations and the evaluation of water extractions. The uniqueness of facility data sources made comparisons and determinations of potential duplication difficult. It was difficult to ascertain whether two nearby facilities are separate operations or if they are the same operation but provided in the data source with different registered business names. Poor data quality could lead to unreliable summaries and analyses and (or) require additional data collection to verify conclusions.
Validity
Facility data validity was measured by how well the data conform to formatting standards. Within the inventory all data are formatted consistently, and missing or not applicable data are indicated by −9999. During compilation much effort was required to ensure this consistent formatting except in facility names. Facility names were included as provided by the data source and misspellings, apparent errors, and name variations were not changed; therefore, some names may not represent the facility name correctly. Not all facility records have been reviewed, and there may be data errors, either inherent from the data source or by the data collection process.
Classification of business types was also an issue and required manual determination in many cases. Some facilities listed as a bottled water facility were later determined to have this as a secondary business line and the primary business code was something other than the codes of interest for this study, such as a water-softening-equipment sales company that also sold bottled water. In these cases, the primary NAICS code was listed as −9999 (not applicable) and the secondary code had the appropriate beverage bottling NAICS code. The “WB_TYPE” listed the beverage bottling type corresponding to the primary or the secondary code when the primary code was −9999. Use of this field requires additional review because of the nonstandard business type in some cases.
Potential implications.—Varied name formats and methods needed to determine facility locations have likely resulted in differing names, which makes searches more difficult. In cases with primary NAICS codes of −9999, additional facility review is needed to determine whether to include the facility in analyses and may require individualized examination of business product lines before evaluating potential withdrawal effects.
Timeliness
Facility data timeliness was measured by how current the data are. Facility statuses were assigned as active-confirmed, active-unconfirmed, closed-confirmed, closed-unconfirmed, former production, and future operation as described in Buchwald and others (2023) (fig. 2). Some information indicating facility status was provided from the data source, and some facilities were independently verified during inventory compilation. However, accompanying metadata to specify the year that the information represented often was unavailable, and the facility statuses and attributes may not be correct for 2023 when the inventory was completed. If the facility was provided from a State agency list, web search, or online map then these were typically marked as active-confirmed. Facilities without an online presence were generally left in the inventory but marked as active-unconfirmed, unless the website link was determined to be a broken link or the domain was for sale, for which those facilities were then marked as closed-confirmed. However, in most cases the year to which this status was applicable is not specified. Therefore, this status may be incorrect for some facilities or may not be applicable to the current year (2023).
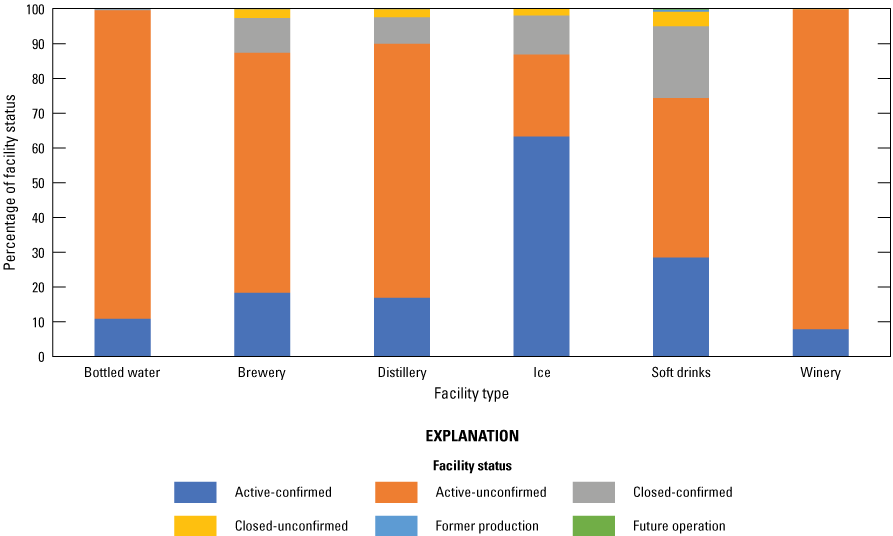
Facility status by beverage bottling type (data from Buchwald and others, 2023).
Of all beverage bottling facilities in the inventory, 92 percent are considered active; however, of these only 17.5 percent have a status as active-confirmed and the rest have not been confirmed as being an active facility (active-unconfirmed). Of all facilities in the inventory, only 22 percent have confirmed statuses of active-confirmed or closed-confirmed. For bottled water facilities, 99 percent are considered active; however, of these only 11 percent have a status as active-confirmed. Of bottled water facilities in the inventory, only 11 percent have a confirmed status of active-confirmed or closed-confirmed. Facility status was investigated for individual facilities for different reasons. For example, many brewery type facilities were checked because many duplicate records were present. These checks were needed to determine which facility record to keep in the inventory. Ice manufacturing facilities have almost 75 percent of records as active-confirmed or closed-confirmed, likely because most ice facilities were determined using national facility lists, such as Regional Ice Manufacturers Association (International Packaged Ice Association, 2024) or company websites like Reddy Ice (Reddy Ice, 2022) for manufacturing locations across the United States. Much effort was required to verify facility status by use of web and mapping searches and was impossible to do for all 43,365 facility records.
It is also important to note the effect that global COVID–19 pandemic may have had on the national inventory timeliness. Although inventory compilation started in 2021 and concluded in 2023, openings of new businesses could have been delayed and others may have temporarily or permanently closed, which likely created a greater shift in business listings. Also, there could have been a lag in reporting status within the source records from data sources.
When data are accessed can affect which facility records are listed and the overall number of facility records listed. The sources used for beverage bottling facility information were periodically updated. For example, some bottled water manufacturers changed their listing of bottling plants between the initial year of data entry in 2021 and inventory review in 2023. However, it was beyond the scope of this project to continually reassess all sources for updates and changes. Therefore, this inventory may not reflect the most up-to-date information and facility status from all sources.
Potential implications.—Many records having an unconfirmed status as active or closed presents difficulties with analyses and would require additional work to verify facility status. Even for facilities with a confirmed status, the year that facility status was checked was not available, so status in 2023 may differ from that specified in the inventory. Facilities sometimes changed products, moved locations, or ceased production, which further complicated verification of status. Knowledge of active facilities would be needed to adequately assess potential effects and determine where withdrawals are occurring across the United States. Also, it might be difficult to make appropriate analyses when all facility and attribute information is likely not representative of the same year.
Accuracy
Facility data accuracy was measured by whether data represented actual conditions. Facility information was subject to variable data quality from the sources providing this information. Multiple reviews were done when possible; however, all information could not be verified for all facilities. Spatially, facility information was collected for each State where available and was assumed to represent beverage bottling operations across the United States, although there are no other complete facility lists for comparison. Limitations and issues from the original data sources propagated throughout other tabular and spatial information in the inventory. For example, if the facility was poorly located, then the dependent information, such as county, hydrologic unit, or water source assignments, may also be incorrect.
Facility locational accuracy was largely unknown, with about 95 percent of facilities with “Unknown” in the “LOC_ACCURACY” field in the inventory table (Buchwald and others, 2023). For these facilities, the location provided was accepted. For some, a geographic information system (GIS) process was used to convert addresses into locational coordinates; however, post office boxes and incomplete addresses (for example, city, State) are not handled well by this method. During data review, it was noted that some facility addresses and coordinate locations were located at the registered agent’s address, parent company, or headquarters location rather than the actual beverage bottling facility location. It is unclear as to how many locations are affected by this inaccuracy. The remaining facilities had locations reviewed and appeared to be accurately located with latitude and longitude within plus or minus 1 to 5 seconds. A small number of reviewed facilities were indicated as “Poorly located” owing to some uncertainties in the provided coordinates. For some facilities, State requirements prohibited publishing actual locations and these facilities were assigned to the county centroid.
Facility names were accepted as provided. Some appeared to have misspellings, but these were not corrected because sometimes the misspelling appeared to be intentional and it would have been too time intensive to verify all facilities. Facility bottling type was provided with the data source. Some checks were performed to see whether facility name agreed with facility type. For example, a spring water company is most likely not a distillery. When these conflicts arose, additional checks were done as time allowed to correct the facility bottling type. However, the accuracy of all facility types has not been verified. Some facilities have been included because a secondary product line falls under the beverage bottling NAICS codes selected for this inventory. For these facilities, the share of business operations devoted to the secondary business type has not been determined. Therefore, beverage bottling operations may be very limited or may be comparable to other businesses with a primary beverage bottling NAICS code classification.
Some information, such as source of water, was estimated based on the facility location when water sources were unavailable from data sources. Of the 43,365 facilities in the inventory, the source of water was determined during data discovery for 1,097 (2.5 percent) facilities and undetermined for 605 (1.4 percent) facilities. For the 41,663 facilities evaluated during inventory compilation, 30,348 (72.8 percent) were located within a public-supply water service area and were estimated to rely on deliveries from the public-supply system for their source of water. For the remaining facilities, 9,145 (21.9 percent) were estimated to rely on groundwater, 738 (1.8 percent) were estimated to rely on springs, 15 (0.04 percent) were estimated to rely on surface-water sources, and the remaining 1,417 (3.4 percent) on a combination of sources. Additionally, facilities located within a public-supply water service area may have their own separate source of water or may rely on public-supply deliveries as a supplemental source of water. Most facilities in this inventory were estimated to rely on public-supply sources but further evaluation may be warranted to determine the accuracy of the water source assignments.
The GIS method described in Buchwald and others (2023) was applied to facilities to test the effectiveness of the method for identifying known water sources. The comparison of water source assignments using the data discovery or the GIS method is shown in table 5. The GIS method does a reasonable job identifying groundwater wells as a water source when facilities are surrounded by groundwater withdrawal sites. The method to assign springs may work well in areas where the facility is surrounded by several springs; however, it is possible the facility supplements or completely taps groundwater for its supply rather than spring water. Also, the spring water source for bottling can be distant from where the actual bottling facility is located; therefore, this GIS method based on proximity becomes less precise. The GIS method was not designed to assign facilities to a “combination of different sources” because it consists of a mix of different sources determined during data discovery.
Table 5.
Number of facilities and percent match for data discovery and geographic information system methods of assigning water source (data from Buchwald and others, 2023).[GIS, geographic information system; --, no data; Water source assignments marked in data discovery as a “combination of water sources” were excluded from the GIS method. The estimation approach assigns the facility location to one of four discrete water source bins (groundwater wells, public supply, springs, or surface-water intakes) or as undetermined. Record counts for water sources marked “Combination of water sources” and “undetermined” are not part of this water source comparison analysis]
Overall, the primary source of water for bottled water facilities was estimated to be public supply (fig. 3). Some of these facilities were also estimated to use wells or a combination of different sources as their source of water. The primary source of water for other bottling types, soft drink, distillery, ice, brewery, and winery facilities, was also estimated to be public supply followed by wells. Additional evaluation would be needed to determine the accuracy of these estimated sources of water.
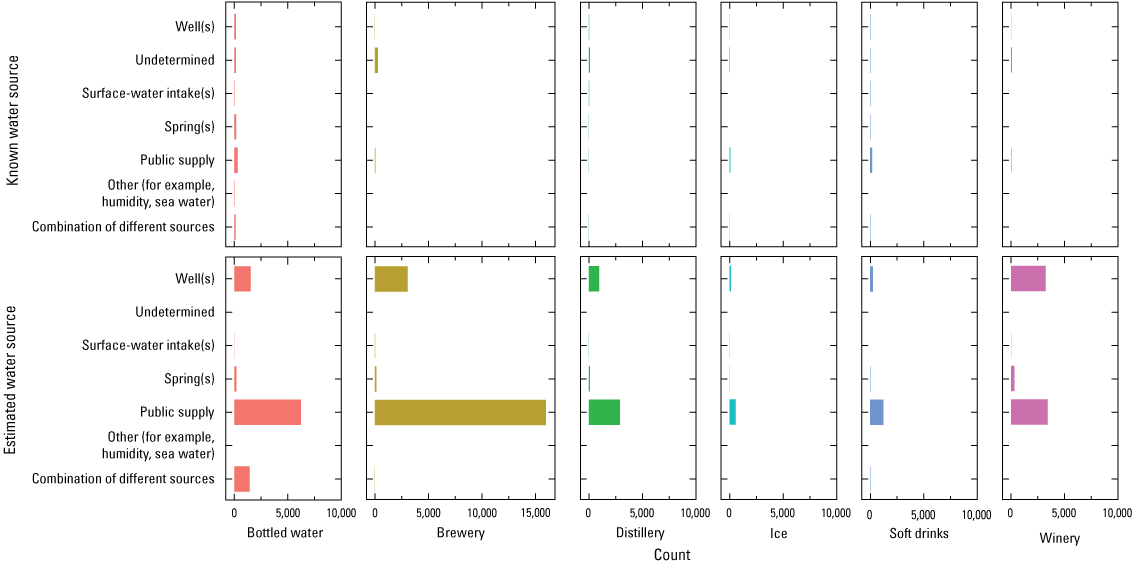
Number of bottling facilities for which the water source was estimated or reported (known) by beverage bottling type (data from Buchwald and others, 2023).
Facility bottling type and other ancillary attributes were accepted as provided from the data sources and no additional verification was done. Ancillary attributes, such as number of employees or facility size, provide information to help contextualize facility information with other similar/dissimilar facilities, to provide characteristics for estimation where water-use information was missing or unavailable, and to provide information about individual facility locations. The attributes may represent individual facilities, the parent company, or the organization as a whole; therefore, these may require some independent verification to ensure consistency and accuracy among facilities if this information is an important part of subsequent analyses. Also, attributes may not represent current facility characteristics or may represent operations for multiple product lines, and isolation of characteristics for water bottling may be impossible. Other attributes may also be important for understanding facility characteristics but were not acquired as part of this study.
Potential implications.—Inaccuracies in facility information might affect conclusions about potential hydrologic effects. For example, an inaccurate location might result in an inaccurate source of water determination and an inaccurate assessment of resource susceptibility. Potential locational issues propagating to other facility attributes could hinder analyses if these other attributes are invalid, which could lead to incorrect conclusions if those attributes are used for other analyses. Further review of facility locations also might be needed to assess potential effects. Most facilities in the inventory were estimated to rely on public-supply deliveries for their source of water; however, facilities within a public-supply water service area may rely on their own source of water in whole or in part. Facilities where the source of water was undetermined or estimated would need additional evaluation to reliably estimate potential effects on water resources. Attributes may represent multiple product lines with insufficient information to determine this information for the beverage types of interest.
Consistency
Facility data consistency was measured by whether the information for each facility was similar; if so, comparisons could be made among different facility bottling types and within facilities of the same type. Facility information was compiled as provided from the sources accessed for this project and any misspellings in facility names were not corrected. For example, “distillery” may be spelled with endings of -iry, -ery, or -ary. Inconsistencies in the spellings and namings, as well as varying brands and ownerships, made it difficult to apply a universal search to select a company brand name. For example, facilities may have similar but slightly different names such as Coke, Coca Cola, Coca-Cola or be named according to the local operating company or may be a brand name. Facilities may have changed ownership and be operating under a national brand but retain the original facility name. Facility names were often repeated locally for a company with multiple locations across large areas of the United States. In some cases, a city or State designation was added after the company name during inventory compilation to reduce the number of duplicate names within the inventory. However, local names sometimes varied so all related facilities may not have been adjusted to reflect the parent company name. As another example, Blue Triton (2023) produces water under many different brand names such as Poland Springs, Ozarka, and Deer Park. When a parent company was apparent, the information was added as an alternate name to assist with the selection of companies operating under the same name, but not all could be identified owing to the many name variations and lack of standardization.
Facilities were added to the inventory and were intended to represent actual manufacturing locations where a bottling or ice product was produced; however, it was often difficult to determine where production happened or where a location had a different purpose such as a warehouse or distribution site. Therefore, facilities in the inventory may not all be representative of manufacturing locations.
Potential implications.—Selection of all facilities belonging to one parent corporation may be difficult with inconsistent naming and therefore difficult to determine potential effects if all facilities of a given type are not selected. Selection of all facilities for a given product type may be incorrect because the inventory may not represent all manufacturing locations or may include nonproduction type locations.
Accessibility
Facility data accessibility was measured by how useable the data are and how accessible and easily discoverable data sources were for finding facility information. Data sources and column descriptions are provided in Buchwald and others (2023) to facilitate ease of use of any information in the facility table (table 1). Facility information from 79 different sources were combined and consistently formatted to create a publicly accessible inventory of beverage bottling facilities. However, not all data sources were consulted, with some information only available in proprietary and restricted sources and other sources unknown or difficult to find. Online searches were helpful for discovering facility information but were time and labor intensive. Some online sources provided little information about water sources or production operations, making facility information difficult to obtain or verify. It is thought that many small businesses, ranging from 28 to 40 percent, do not have a website (Jordan, 2021; Olson, 2022) for various reasons including lack of technical capabilities, financial inabilities, disinterest in growing the business, or that the facility holds the local market with no competition.
Potential implications.—The absence of a complete publicly available bottling facility inventory meant that potential effects of water extractions might be missed where facilities exist but were not captured in the inventory. The lack of websites for small businesses is a limitation to identify missing facilities, confirm status of known facilities, or learn details about beverage bottling operations.
Water-Use Information
Information about water-use quantities and sources of water are needed to assess potential hydrologic effects of extracting water for beverage bottling operations. Water-use amounts were compiled and published in the water-use table, whereas sources of water were included in the facility table (Buchwald and others, 2023).
Water-use data were obtained for 257 of the overall 43,365 facilities inventoried (0.6 percent), and water-use data were obtained for 159 of 10,192 facilities (1.6 percent) that produced bottled water. The data contained 1,929 water-use records (years), including 59 proprietary records not provided in Buchwald and others (2023). The estimated quantity of water used annually ranged from less than 1 gallon per day to 11.3 million gallons per day (Mgal/d). Monthly water-use data were available for a total of 1,459 years at 153 of these 257 facilities. The data included 618 water-use records (years) for 159 bottled water manufacturing facilities, which was an average of about 3.9 years per facility that had records, and the estimated quantity of water used annually ranged from less than 1 gallon per day to 1.8 Mgal/d. Monthly water-use data were available for 420 years for 75 of 159 bottled water manufacturing facilities with water-use data.
Based on limited available water-use data (0.6 percent of total facilities), the distributions of reported annual water use for inventoried facilities varied by beverage bottling category (fig. 4). Median annual water use was 0.0435 Mgal/d (43,500 gallons per day) for 618 annual values reported for 159 facilities producing bottled water. The bottled water facility median reported value was lower than the median annual water use reported for the other beverage bottling categories: 0.0863 Mgal/d for 60 annual values reported for 10 ice manufacturing facilities; 0.114 Mgal/d for 1,164 annual values reported for 65 soft drink manufacturing facilities; 0.281 Mgal/d for 19 annual values reported for 12 distilleries; and 2 Mgal/d for 68 annual values reported for 11 breweries. No water-use data were available for wineries.
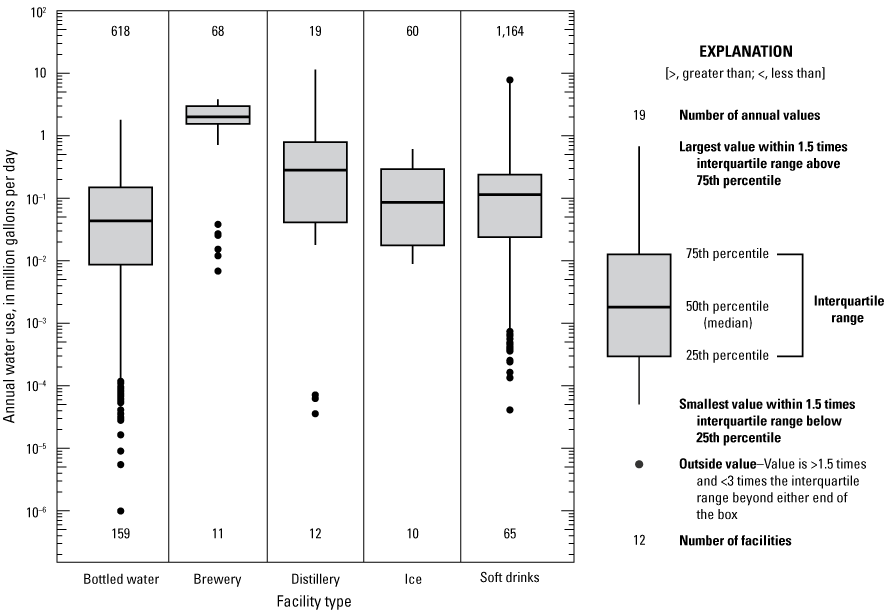
Distributions of reported annual water use for facilities by beverage bottling category (data from Buchwald and others, 2023)
Given the small percent of inventoried facilities with available water-use data (0.6 percent of all beverage bottling facilities and 1.6 percent of bottled water facilities), methods for estimating water use were explored. Several facility attributes including employment, sales, facility size, and fleet size were hypothesized to be related to quantities of water use (fig. 5). Approximately 90 percent of all inventoried beverage bottling facilities had business operating attributes (such as counts of employment, sales, and facility size); however, fewer of the facilities having water-use data available also had business operating attributes. Some additional work was done to add facility attributes for facilities with water-use data as part of the version 2 update (Buchwald and others, 2024). Fifty-one of 159 bottled water facilities (32 percent) with water-use data also had specific employee counts, and 123 of 257 beverage bottling facilities (47.9 percent) with water-use data had specific employee counts. Where specific employee counts were absent but the range of employees (EMPL_RANGE, table 1) was populated, the midpoint (median) of the employee range was used. Median annual water use and employee counts by beverage bottling type for the 127 facilities having water-use and employment data are shown in figure 5. Considerable variability is apparent in the relation of water use and employment, particularly in the lower range of employment. Some outliers were observed, specifically the lower point (39 employees and 1 gallon per day use), which was likely an incomplete reporting of use. Also, several points with relatively large use (approximately 0.03 to 1 million gallons per day) but only 2–4 employees points in upper left of graph in figure 5 seemed unrealistic, and most of these were facilities having their water use estimated as a water-withdrawal permit limit or water right, which likely exceeded actual water use.
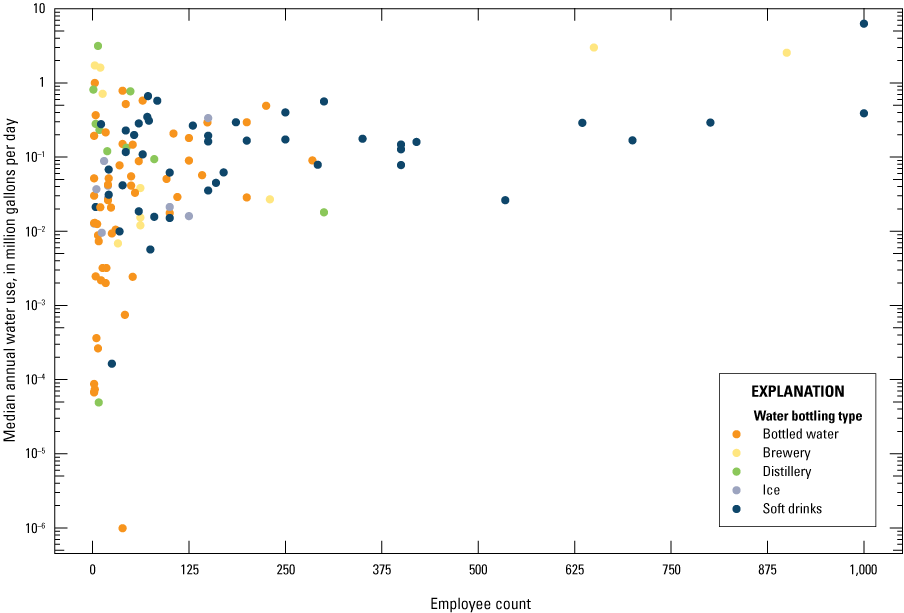
Distribution of median annual water use and employee counts by water-bottling type for the 127 beverage bottling facilities (data from Buchwald and other, 2023).
Completeness
Water-use data completeness was measured by how many facilities have water-use information and accompanying facility location, type, and other attributes. Completeness includes whether water-use data represent facilities spatially across the United States and temporally with water-use data available annually and monthly over the time period of interest. Finally, completeness also includes how well the water-use data represent withdrawal amounts at each facility and for each bottling type.
Bottling facility information was compiled for all States and territories in the United States; however, water-use data were only acquired for facilities in 34 States (fig. 6A). The number of beverage bottling facilities with water-use data ranged from 1 each in Alabama, Rhode Island, South Carolina, Tennessee, and Vermont to 55 facilities in Texas. The number of years of water-use data for beverage bottling facilities ranged from 1 each in Alabama, Kentucky, New Hampshire, Rhode Island, and Vermont to 66 years of data in Texas (fig. 6B). For bottled water facilities, water-use data were available in 31 States (fig. 7A). The number of bottled water facilities with water-use data ranged from 1 each in Alabama, Indiana, Kansas, Kentucky, Rhode Island, South Carolina, Tennessee, Utah, and Vermont to 17 in Massachusetts. The number of years of water-use data available for bottled water facilities ranged from 1 year in Alabama, Kentucky, New Hampshire, Rhode Island, Virginia, and Vermont to 40 years in Texas (fig. 7B).
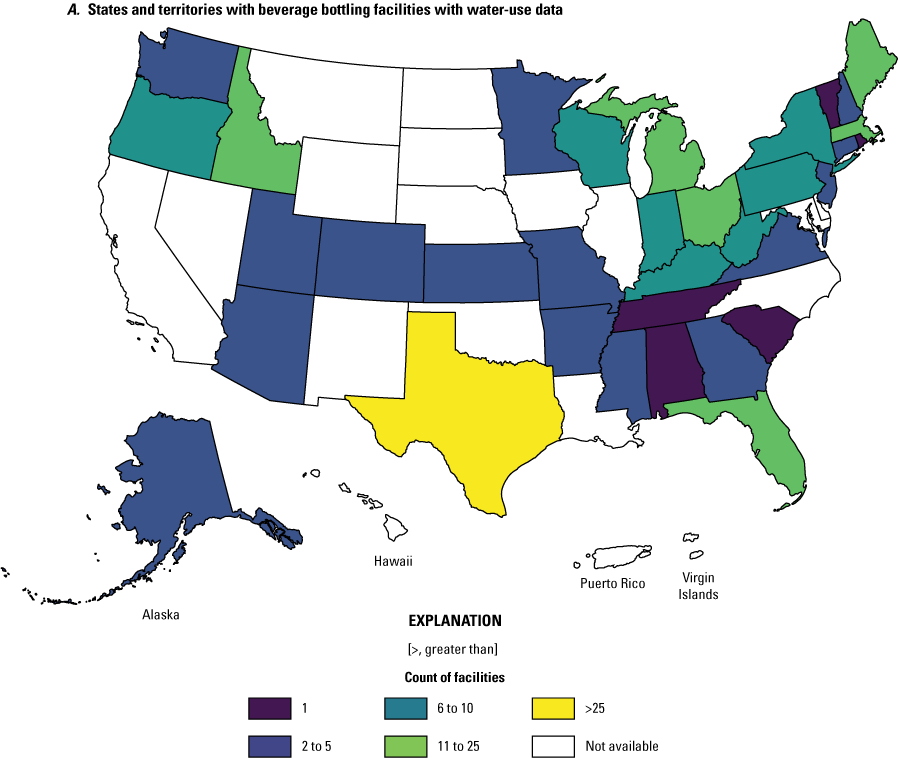
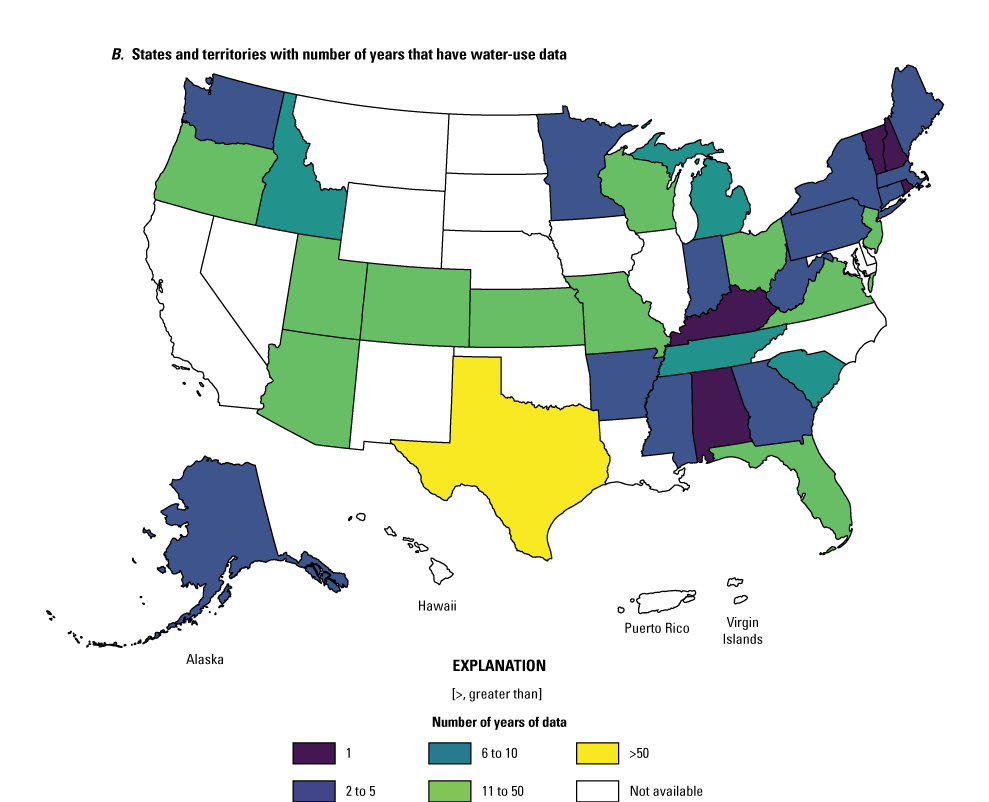
Water-use data for beverage bottling facilities in the United States. A, Number of beverage bottling facilities with water-use data. B, Number of years of water-use data for beverage bottling facilities (data from Buchwald and others, 2023).
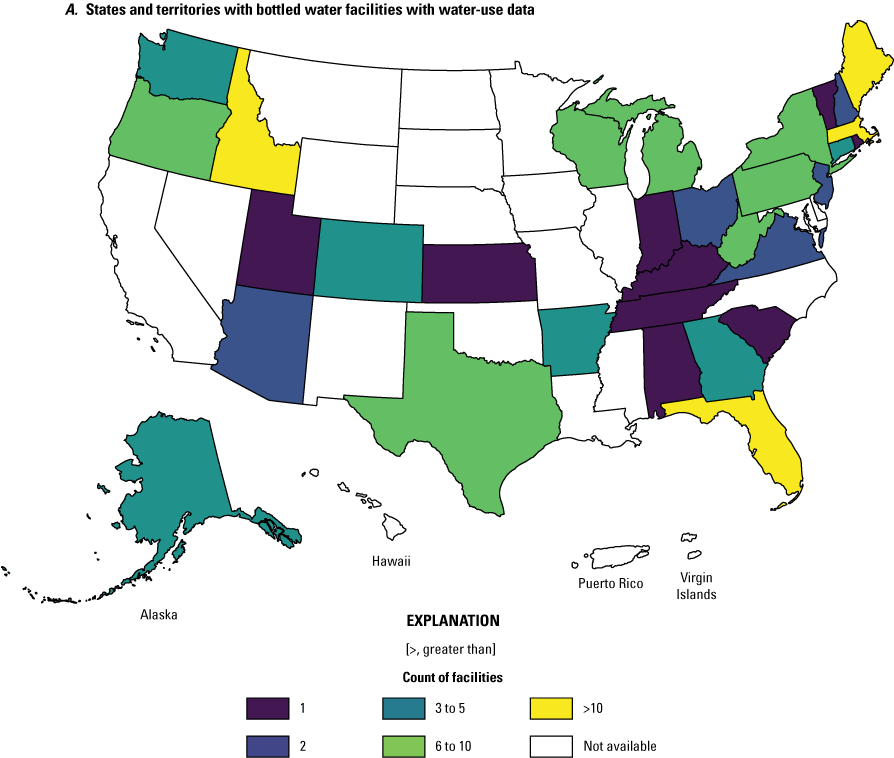
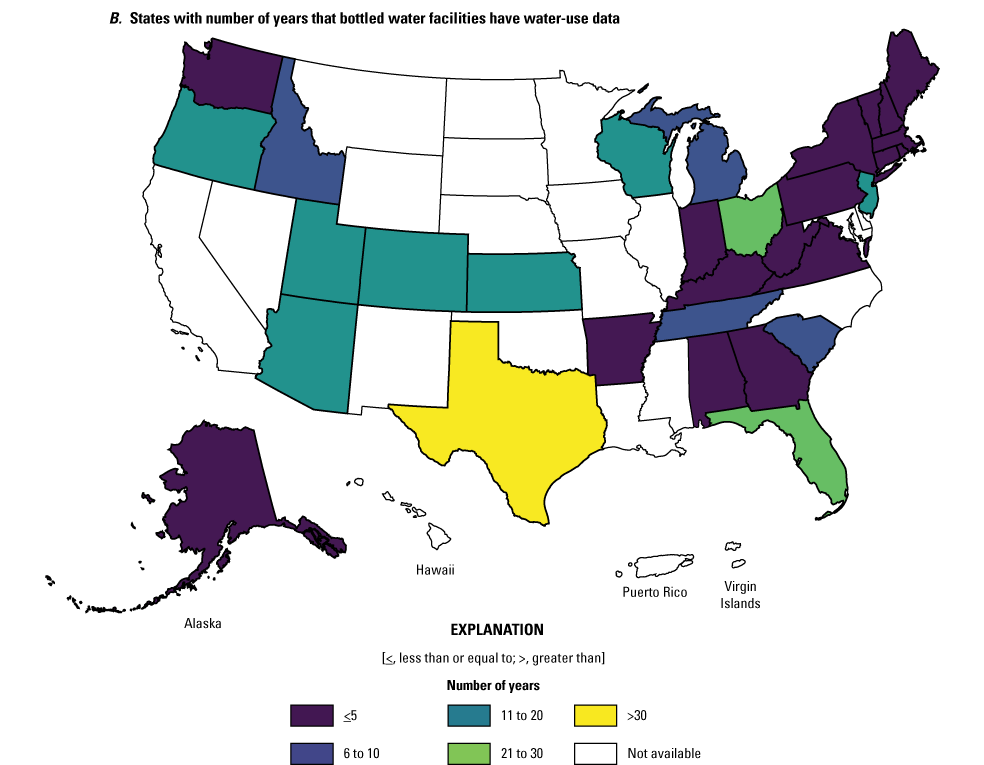
Water-use data for bottled water facilities in the United States. A, Number of bottled water facilities with water-use data. B, Number of years of water-use data for bottled water facilities (data from Buchwald and others, 2023).
Thirty-four States had at least one facility with water-use data, but water-use data were not available for 20 States and territories, many of which were in the western part of the United States. The number of bottled water facilities with water-use data were compared to the total number of bottled water facilities by State (fig. 8). In almost all States with water-use data, fewer than 10 percent of bottled water facilities have water-use data. Water use is available for more than 10 percent of inventoried bottled water facilities in Idaho, Massachusetts, Maine, and West Virginia.
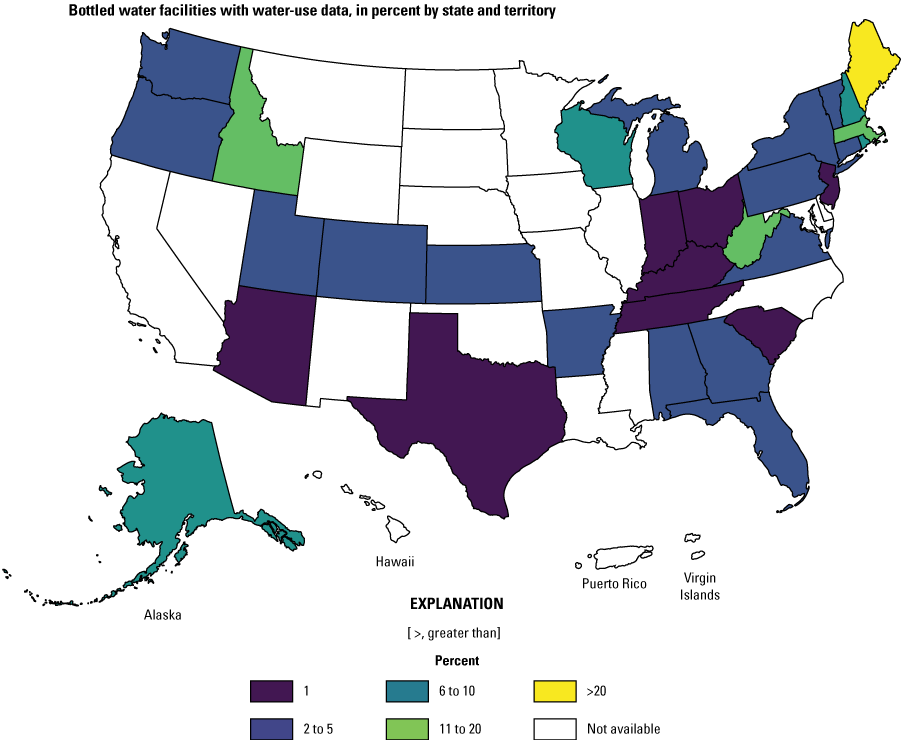
Percent of bottled water facilities with water-use data by State (data from Buchwald and others, 2023).
Water-use data could only be acquired for about 0.6 percent of all facilities in the inventory (Buchwald and others, 2023). Water-use data were compiled for 257 facilities (4 facilities have restrictions on releasing site-specific data as of 2023) as annual and (or) monthly withdrawal amounts for years ranging from 1955 to 2022 (fig. 9). No facilities had water-use data for all years 1955–2022; however, 8 soft drink facilities in Texas had water-use data for 40–50 years and 1 bottled water facility in Texas had water-use data for 38 years. No years had data for all 257 facilities having water-use data. Annual water-use data were available for one facility during the time period from 1955 to 1959. Most annual data were available for the years 2017 to 2020, with 82 facilities having water-use data for 2020. Data were primarily collected in 2019 and 2020, resulting in sparse data for 2021 and 2022. Availability of monthly data providing information about water usage throughout the year ranged from one facility with monthly water-use data in 1960 to 60 facilities with monthly data in 2018 and 2019.
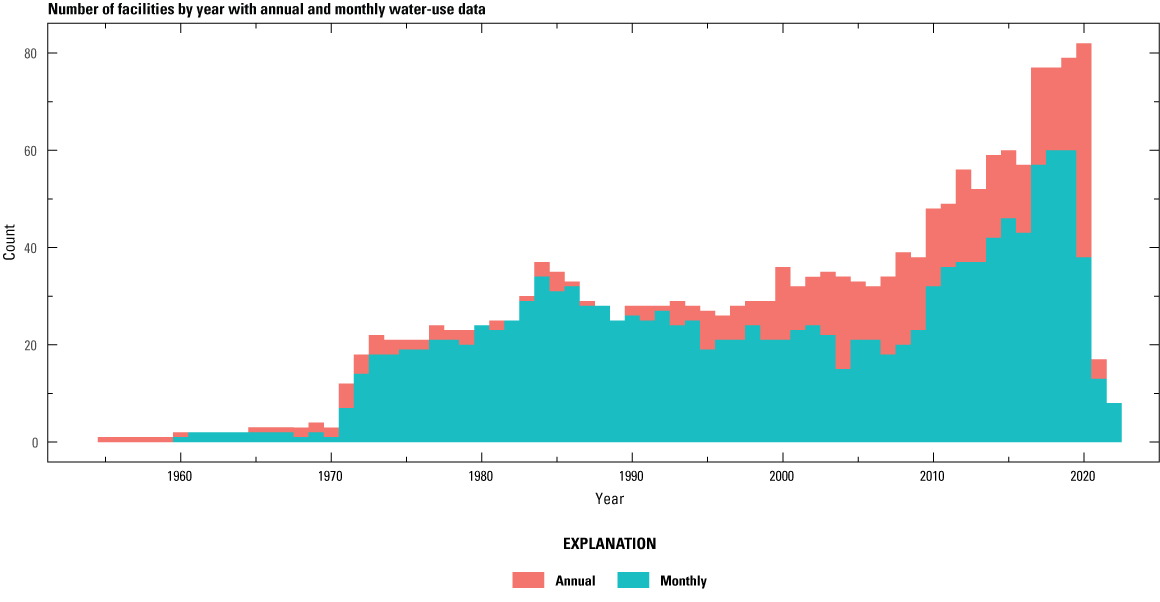
Number of facilities with annual and monthly water-use data by year (data from Buchwald and others, 2023).
Water-use data availability was also variable depending on the type of beverage bottling facility (table 6, fig. 10). Given that the primary focus of the overall project was on bottled water, emphasis was placed on acquiring data for bottled water facilities, and less so for the other types of bottled beverages included in Buchwald and others (2023). As a result, the dataset had the most water-use data values for bottled water facilities. For example, withdrawal data were available for 70 bottled water facilities in 2020 in the inventory. Data were more consistently available over time for soft drink facilities with 20–36 facilities having water-use data from 1973 to 2018 (fig. 10). Very little water-use data for breweries, distilleries, and ice facilities were included in Buchwald and others (2023) and no water-use data were included for wineries.
Table 6.
Number and percent of facilities with water-use data by bottling facility type (data from Buchwald and others, 2023).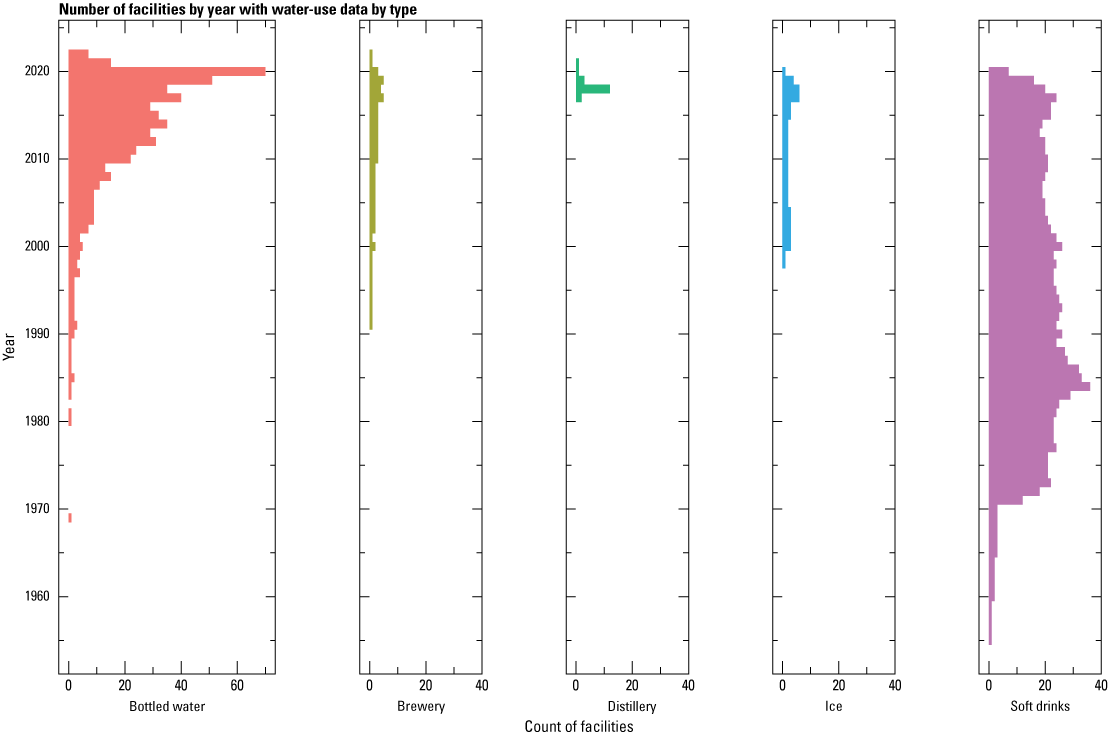
Number of facilities with water-use data by year and type of facility (data from Buchwald and others, 2023).
The source of water, whether local self-supply or public-supply deliveries, used by the bottling facilities was known for most facilities (97 percent) with water-use data because the source of water was usually reported with the water-use records (fig. 11). About 54.1 percent of facilities relied on self-supplied sources (wells, springs, surface water, or other) (fig. 12). Other facilities rely on public supply (28.5 percent) or a combination of different sources (15 percent). However, facility-level, public-supply delivery data for individual customers may or may not be collected by the public-supply system and were rarely publicly available. Public-supply withdrawals were reported for the public-supply facility and generally not for individual users or customer types within the system. Water-use amounts for 19 facilities that received some water as deliveries from a public water system may be incomplete because detailed information was unavailable as to when and what extent the beverage bottling facility relied on local supplies in addition to water from the public-supply system. The source of water for other bottling types with water-use data varies and was primarily public supply for soft drink and brewery facilities, wells for ice manufacturing facilities, and surface water for distilleries (fig. 12).
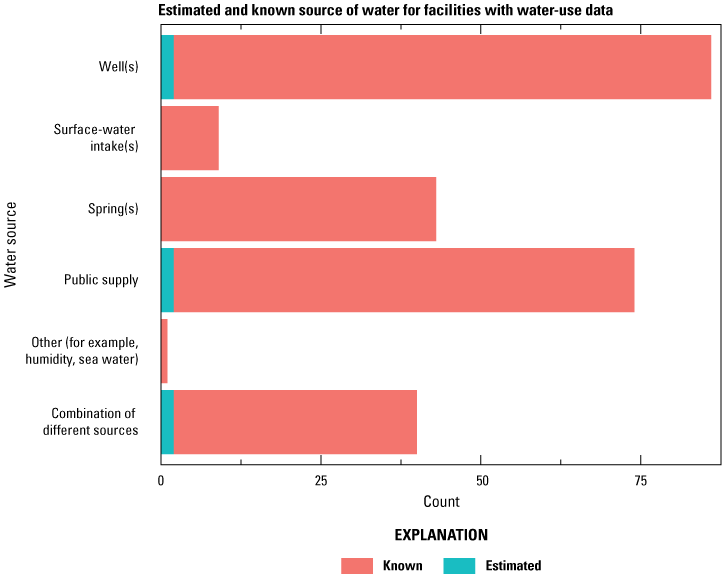
Number of bottling facilities with water-use data for which the water source was estimated or reported (known) (data from Buchwald and others, 2023).
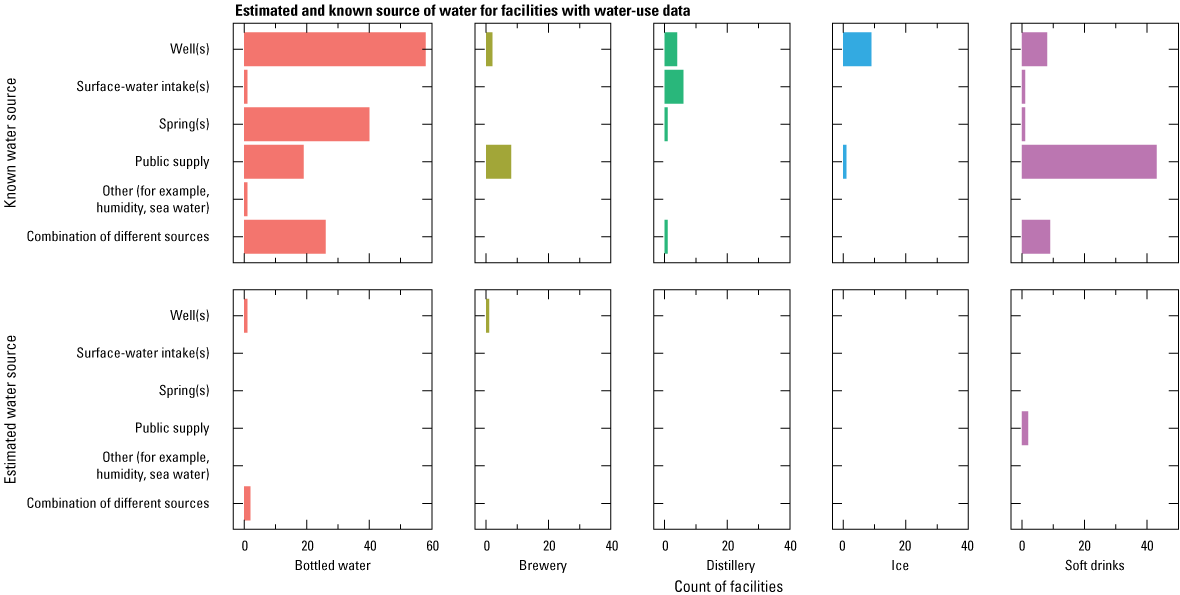
Number of bottling facilities by beverage bottling type with water-use data for which the water source was estimated or reported (known) (data from Buchwald and others, 2023).
Attributes for facilities provide a means for comparisons of facility size, employee counts, and sales ranges and could be useful for estimating missing water-use data. However, many of these attributes were unavailable for facilities with water-use data (fig. 13). Of the 8 facility attributes, the year the facility was established was most available but was still missing for more than 75 percent of facilities with water-use data. These ancillary attributes were provided for facilities from Data Axle (2023). Because facilities with water-use data were compiled primarily from State agencies, attributes were not available for most of these facilities in version 1 (Buchwald and others, 2023).
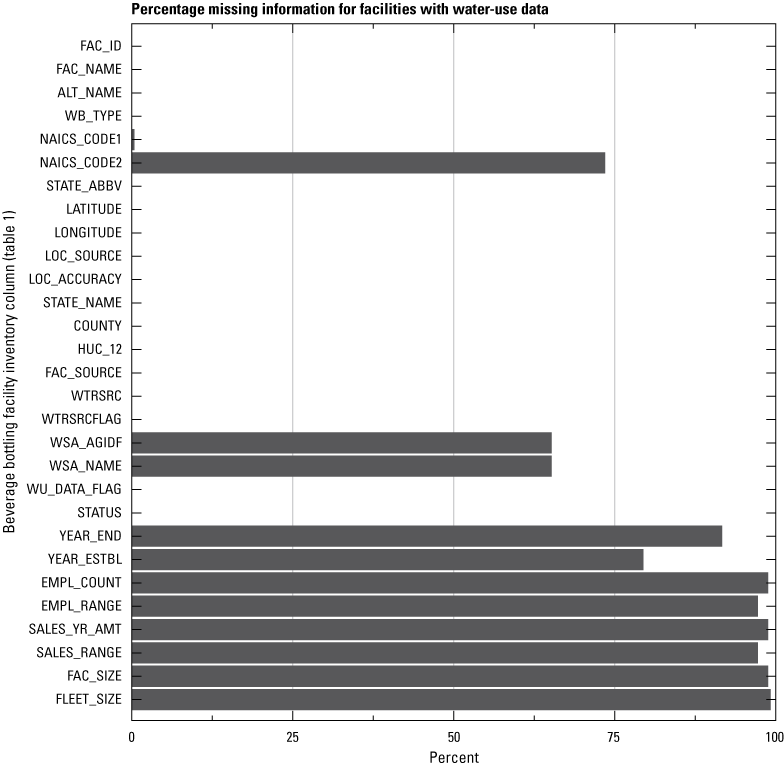
Percent missing information for facilities with water-use data (data from Buchwald and others, 2023). See table 1 for column descriptions. WSA_AGIDF and WSA_NAME are only assigned to facilities with a public-supply source and are assigned as –9999 (missing) for facilities using other sources.
Some efforts were made to match attribute information to facilities with water-use data for the version 2 update (Buchwald and others, 2024). However, these matches needed to be done using name and (or) location matching. Business data sources use their own unique identifiers that were not readily joinable to other datasets. This extra effort was considered worthwhile owing to the usefulness of facility attributes. The percent of missing attributes for facilities with water-use data by bottling type in the original version 1 inventory (Buchwald and others, 2023) and after work to match sites with additional attribute information in version 2 (Buchwald and others, 2024) is shown in figure 14. The highest increase in attribute information percentages was observed for breweries; however, there were only 11 breweries in the inventory with water-use data. In Buchwald and others (2023), most facility characteristic attributes were only available for two breweries. In the subsequent effort, attributes were added for another eight breweries contributing to the large change in percent. Bottled water facilities constituted the largest number with water-use data in the inventory (155 facilities) and had the lowest change in percentages; however, attributes were added for about 50 facilities.
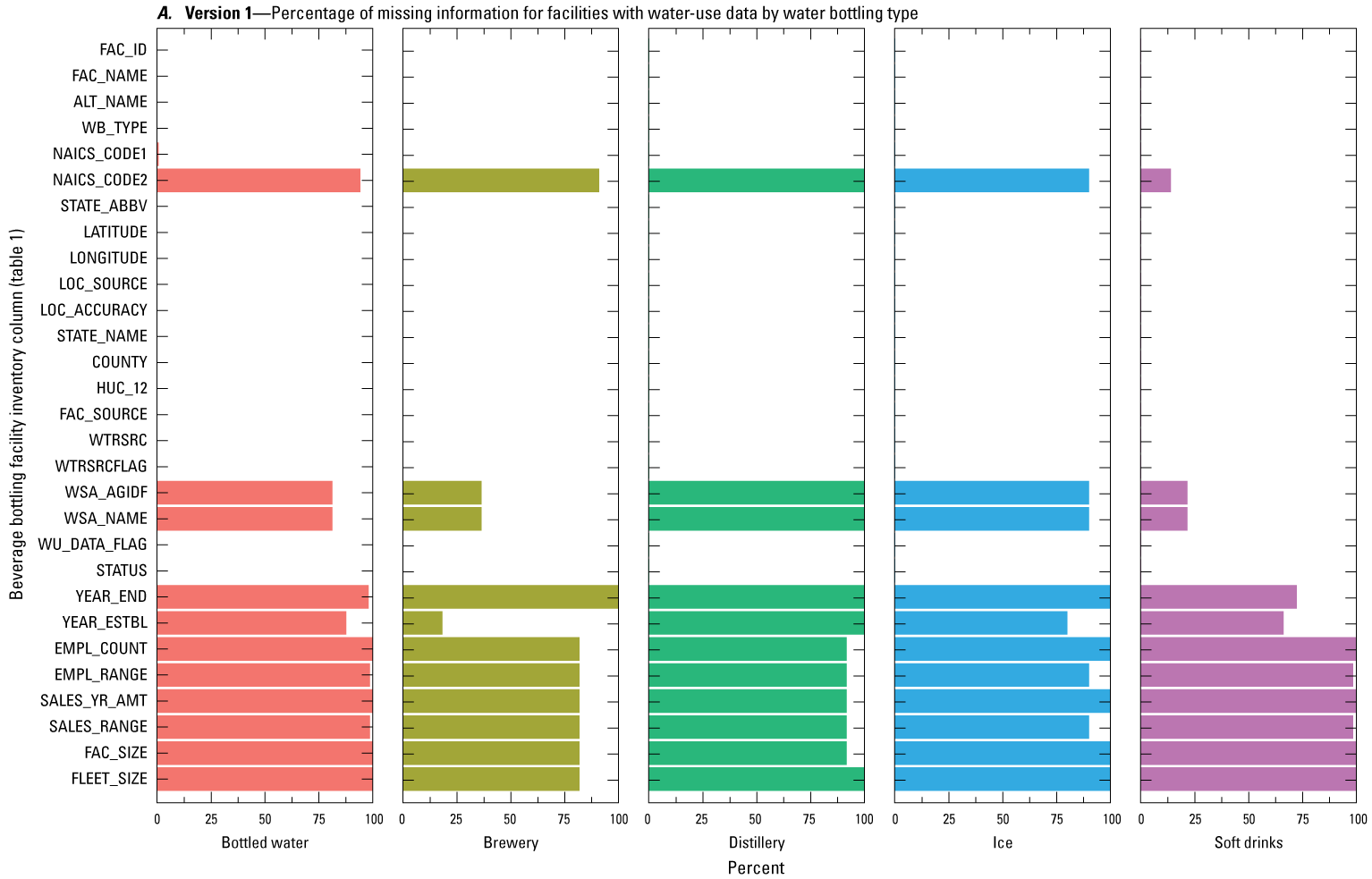
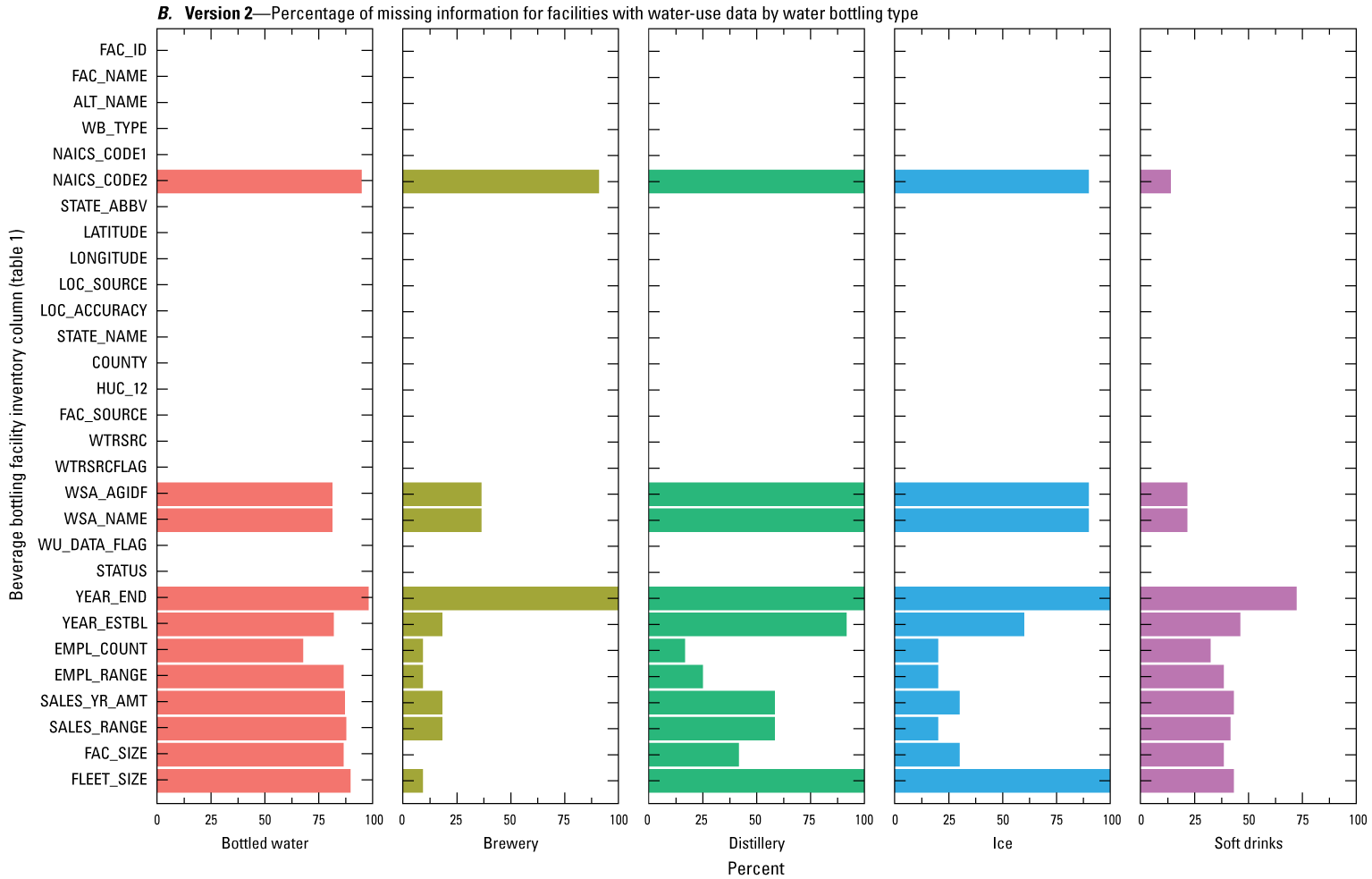
Percentage of missing information for facilities with water-use data by beverage bottling type. A, Inventory in version 1 (Buchwald and others, 2023). B, Inventory in version 2 (Buchwald and others, 2024). See table 1 for column descriptions. WSA_AGIDF and WSA_NAME are only assigned to facilities with a public-supply source and are assigned as –9999 (missing) for facilities using other sources.
Potential implications.—Determination of potential hydrologic effects is dependent on knowledge of withdrawal amounts and the source of water. Publicly available water-use data were very sparse for all beverage bottling types and not available at all for wineries. Water-use data were primarily acquired for self-supplied facilities; therefore, the distribution of water use by water source may not be representative of the entire beverage bottling industry. Beverage bottling facilities relying on publicly supplied water were generally not required to report water use to State agencies; therefore, the characteristics of water usage by these industries were not captured fully in the water-use dataset. Water usage for facilities that relied on public-supply deliveries was combined with all the other users within the water service area, and thus, any effects from individual facilities would be difficult to understand. Water usage for facilities within a water service area with their own supply may be missed unless additional evaluations are done for facilities with an estimated source of water.
More water-use data were available for 1 year for bottled water facilities; however, for soft drink facilities, withdrawal data were available for multiple years but at fewer facilities. Given the limited water-use data available in Buchwald and others (2023), more data may need to be acquired to evaluate the effects of withdrawals for bottling at a national scale. Another option would be to use available facility attributes for facilities with water-use data to estimate water use for other facilities; however, attributes were largely missing for these facilities with water use. These and other potential predictors of withdrawals for water bottling would need to be acquired for facilities with water use to be able to estimate water use for other facilities. The spatial gaps also make determination of potential hydrologic effects difficult for large areas of the United States.
The source of water for facilities with water-use data was known for most of the withdrawals, with most relying on self-supplied sources of water. In these cases, further investigations could be done to evaluate potential effects on surrounding water levels and surface flows. Close to one-third of the facilities for which water-use data were available (28.5 percent) relied on public-supply deliveries. Determining or acquiring the quantity of water delivered to bottling facilities from public-supply systems was difficult because the withdrawals for bottling facilities were only one part of total withdrawals by the public-supply water system.
Uniqueness
Water-use data uniqueness was measured by the presence of duplicate facility water-use information. Water-use data for beverage bottling facilities were compiled primarily from State agency sources and were not available from multiple sources for the same facility. These water-use data were compiled as provided and no duplication existed.
Potential implications.—There were no potential implications identified.
Validity
Water-use data validity was measured by how well the data were consistently formatted and conformed to standards, and the amount of effort needed to reconcile conflicting units and to convert all data to similar values. Within the inventory all data have been formatted consistently, and missing or not applicable data were indicated by −9999. During compilation much effort was required to ensure consistent formatting. Water-use data were provided in different units, requiring conversion to consistent units for use. Some water-use data were provided by individual source withdrawal locations and required summation to the facility level for publishing in Buchwald and others (2023).
Available water-use data were compiled for beverage bottling facilities but metadata describing these data were largely unavailable and variable. Metadata from some sources indicated whether withdrawal values were estimated, metered, or reported from a facility to the reporting agency (fig. 15); however, metadata from the source agency often did not indicate whether facilities measured or estimated the withdrawal amounts, and the method of estimation was not provided with the estimated data values. Other withdrawal estimates may be a permitted or capacity value and may not represent actual withdrawal amounts. In some cases, no information was available on how the withdrawal value was determined. Additionally, some facilities provided more than one method because it differed by withdrawal source or reporting year. The water-use data for bottled water facilities were primarily metered or reported. Water-use data for breweries and ice facilities were also primarily reported. Water-use data for soft drink facilities were about equally divided between estimated and metered data.
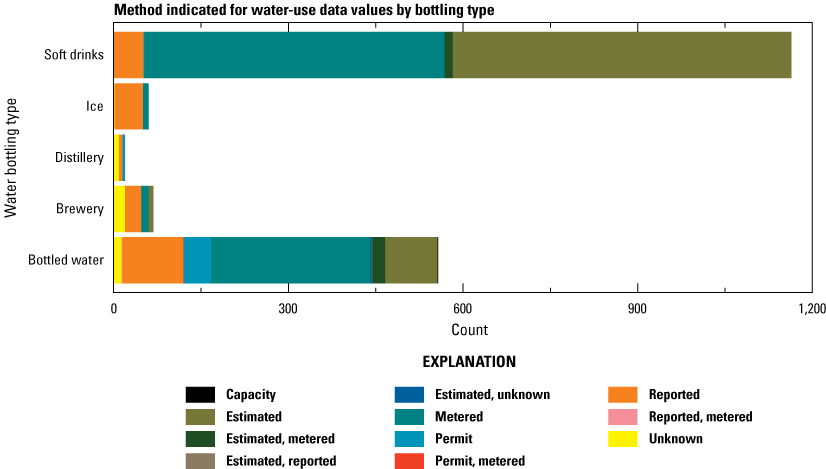
Method of determination of water-use data (data from Buchwald and others, 2023). Facilities may have more than one method if it varied by withdrawal source or reporting year.
Potential implications.—Water-use values included some information about how the amounts were determined; however, some were capacities or permitted values that do not represent actual withdrawals. Other values were estimated and may not represent actual withdrawal amounts. Therefore, users of these data may need to evaluate the quality and (or) usefulness of the withdrawal data owing to variability in the methods used to measure or estimate the water-use values.
Timeliness
Water-use data timeliness is indicated by whether the data represent current up-to-date conditions, or the time range of interest to the user. Water-use data were collected for as many years as were available, with the most recent year of data available for 2022; however, only eight facilities had data for that year (fig. 9). Most data were available for 2020, which was the year of primary focus for water-use data collection. Water-use data were available for multiple years or for just one individual year (fig. 10).
Ancillary data such as employee counts and facility sizes were from a different data source than the water-use data. Ancillary values reflect the year Data Axle (2023) acquired the information, which is variable and unknown. Therefore, the ancillary data may or may not represent the same year(s) as the withdrawal data. In addition, the ancillary data may not be representative of facility characteristics for all years of operation at the facility. Where only 1 year of data was available, withdrawal amounts may not be representative of typical operations at the facility owing to other factors that may affect water-use amounts.
Potential implications.—Water-use data were compiled for available years with some facilities having water-use data for 1 or more years. However, the amount of water-use data was very limited temporally and spatially. No facilities had data for all years and most had no data for the most recent year (2022). Limited temporal range in available water-use data will limit the data user’s ability to estimate trends in withdrawals and (or) may skew the estimates of “average” withdrawals. Ancillary attributes represent different years that may not coincide with years with water use and may also limit or affect usefulness of the data to estimate withdrawals at facilities over time because ancillary attribute changes may not be captured in Buchwald and others (2023).
Accuracy
Water-use data accuracy is measured by whether data represent actual conditions. Water-use data were acquired for only 0.6 percent of facilities in the inventory and 1.6 percent of bottled water facilities (table 6). Four other beverage bottling facilities provided water-use data; however, there were data-sharing restrictions preventing the release of site-specific data so these data can only be used in an aggregated form.
Some withdrawal data were estimated, whereas other data were measured but with unspecified methods resulting in unknown accuracy for the data values. As described in the “Validity” section, the varied measurement and estimation methods may affect the accuracy of the available withdrawal data. Quality assurance checks were done to determine agreement between the provided data values when annual and monthly data were provided. For 17 facilities with annual and monthly water-use data, the total of the monthly values did not equal the reported annual value. Some facilities had multiple years where monthly and annual values did not agree. Reconciliation of these differences was not possible in all cases. Therefore, differences greater than 5 percent were noted in the water-use data table (Buchwald and others, 2023).
Because only 0.6 percent of facilities have water-use data, these data may not be representative of the water-use characteristics of the wide range of facilities across the United States. The small sample of 127 facilities that have water-use and employment data have generally larger employment than the full set of 39,441 facilities with employment data (fig. 16). In that sample, the median employment ranged from 2 to 12 times as large; for example, the median employment for the sample of 54 bottled water facilities with water-use and employment data was 24, whereas the median employment for the set of 9,029 bottled water facilities with just employment data was 2.
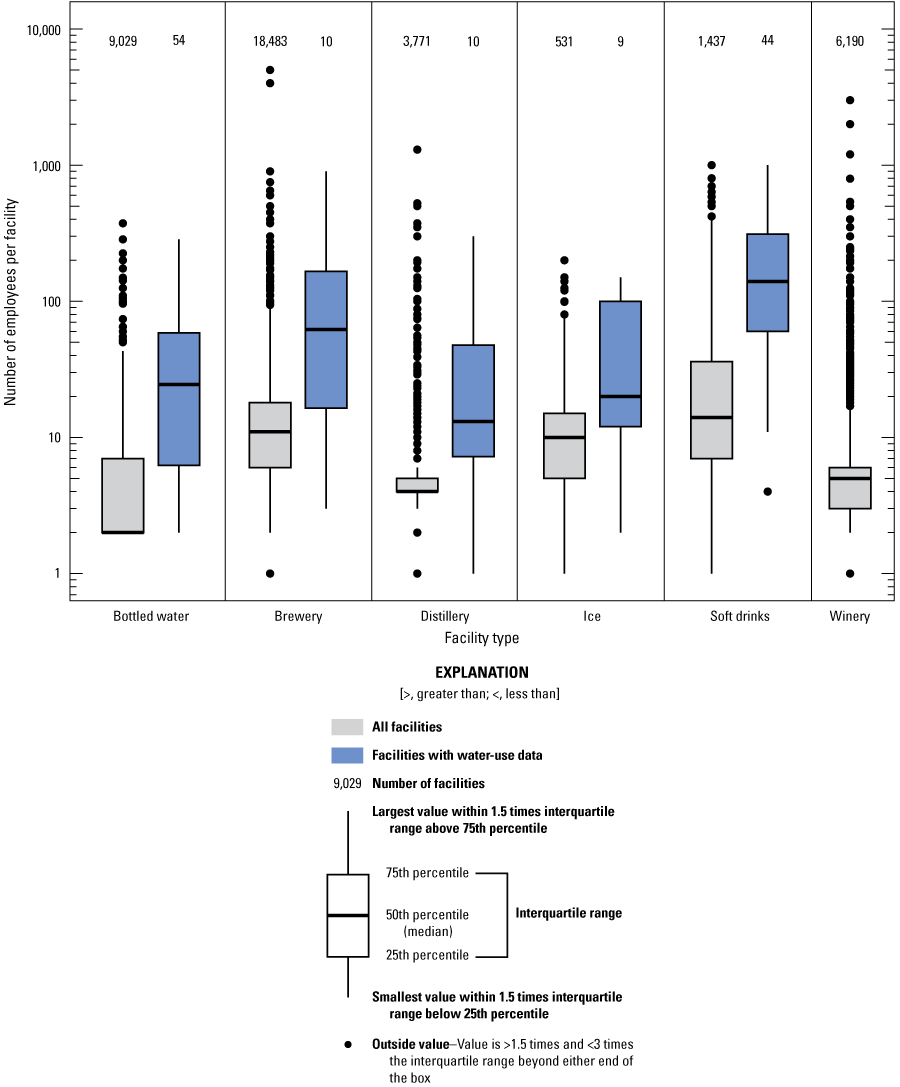
Distribution of number of employees by beverage bottling facility type for all facilities and facilities with water-use data (data from Buchwald and others, 2023). Note that there were no wineries with water-use data.
Potential implications.—Additional water-use data are needed to adequately determine the potential hydrologic effects from withdrawals for bottling facilities. Limited withdrawal data representative of facilities and limited information on the accuracy of available withdrawal data may result in uncertainty in estimated withdrawals for bottled water. In addition, the acquired water-use data may not be representative of the characteristics for all facilities across the United States.
Consistency
Water-use data consistency was measured by whether the information for each facility was similar and, if so, comparisons could be made between water-use amounts among different facility bottling types and within facilities of the same type. When the water-use amounts differ for various reasons, then comparisons are problematic and may lead to misleading conclusions.
Available water-use data were compiled as provided; however, attempts were made to determine whether the water-use amounts were for actual production of a product or for water-use needs at distribution or warehouse facilities. Some water-use data were not included in Buchwald and others (2023) when it was (1) apparent that the facility was not a production location, or for years after production of a product ceased at the facility location; or (2) if there was not a clear indication of the plant receiving the water. Therefore, for facilities, water-use data were compiled to be as representative as possible of water needs for production of the beverage or ice product.
An additional factor affecting analysis of water-use amounts was that values may represent water use for multiple product lines rather than just the beverage bottling product. Water use was provided for each facility but was not divided into amounts for different manufactured products or processes within the facility; therefore, these data may not be comparable among facilities. For example, some facilities listed as manufacturing a beverage product may also have a nonbeverage bottling product manufacturing line such as water softening equipment, but the reported withdrawal was a combined total for the plant.
Potential implications.—To evaluate potential effects of withdrawals for beverage bottling, withdrawals were needed for production facilities and for beverage products that incorporate water into a product. However, determination of if and when a facility produces a product was difficult. Likewise, water-use amounts were provided for the facility and not by individual product line. Therefore, water-use amounts may not be consistent from facility to facility and conclusions for potential effects may be inaccurate or misleading.
Accessibility
Water-use data accessibility is measured by how useable the data are and how accessible and easily discoverable data sources were for finding facility water-use information. Data sources and column descriptions were provided in Buchwald and others (2023) to facilitate ease of use of any information in the water-use table. The “FAC_ID” field (facility identifier) (table 1) provided a unique identifier to link each facility in the facility table to the water-use information table in Buchwald and others (2023). The water-use data provided by facility in the inventory were released publicly for all but four facilities in a format that was useable and available for further analyses. Overall, water-use data were only available for a small number of facilities (0.6 percent) in the inventory.
Much effort was expended to locate State agencies responsible for beverage bottling facility permitting and water-use reporting programs. Every effort was made to request water-use data from these programs or from other online sources. However, water-use data were largely unreported and not publicly available for most of these facilities. This lack of available water-use data can potentially be attributed to (1) States not having a reporting program, (2) facilities withdrawing less than a State reporting threshold, (3) facilities relying on water delivered from a public-supply water system, or (4) water withdrawal data not being publicly available. Water-use data are not readily available in States where there is not a requirement to report water-use amounts or where facility withdrawals are small and fall below reporting requirements. Collection of data in these cases may only be possible by individually contacting each facility and requesting water-use amounts. In addition, some agencies or facilities may collect water-use data but do not release this information publicly and estimation may be the only means for determining water-use amounts.
Potential implications.—With sparse water-use data, having information for four facilities being publicly unavailable further reduces the amount of information needed to assess potential effects from extractions for beverage bottling operations. Data provided in Buchwald and others (2023) are useable, provided in a machine-readable file, with associated metadata defined; however, owing to unreported and unavailable water-use data, analysis of the data may be limited.
Great Lakes Regional Assessment Inventory Case Study
During the development of the inventory, the Great Lakes regional assessment evaluated selected facilities within the Great Lakes Basin, hydrologic unit 04 (U.S. Geological Survey, 2024) covering Michigan and parts of Illinois, Indiana, Minnesota, New York, Ohio, Pennsylvania, Vermont, and Wisconsin. Of the 2,852 facilities in the Great Lakes region, 826 facilities with an undetermined source of water were evaluated for completeness and accuracy. Online web searches were done to confirm facility location, facility/owner name, business status, product manufactured, and whether any duplicate records existed within the inventory. These online searches also identified facilities that were missing from the inventory. The Great Lakes regional assessment attempted to determine a source of water when the information was missing. Water source for a facility was determined through online web searches of facility name or beverage bottlers within a county, using comparisons with water sources of other nearby facilities, such as U.S Environmental Protection Agency (2023), or was left as undetermined when there was insufficient information.
Concurrent with this effort in the Great Lakes region, development of the national inventory continued with identification of water sources, addition of missing facilities, and removal of duplicate records. Some issues and corrections identified in the Great Lakes regional assessment were made before the inventory was finalized; however, the Great Lakes assessment was not completed before the national inventory was published. Therefore, some changes were made to version 2 (Buchwald and others, 2024) to correct water sources, remove inaccurate facilities, and add missing facilities.
Of the 826 facilities in the Great Lakes region with an undetermined source of water, 145 facilities were assigned to a public-supply, groundwater well, surface-water, or spring source. The remaining 681 facilities were either flagged for possible removal or the source of water could not be estimated. The assignments during the Great Lakes assessment were compared to the water sources in the national inventory that were estimated using the GIS method. Eighty facilities were assigned to a well source using both methods. Another three facilities were assigned to a public-supply source using both methods. The remaining 62 facilities were assigned different sources using the Great Lakes assessment method or the national inventory GIS method. These facilities would need further assessment to determine the most likely source of water.
The Great Lakes regional assessment identified 596 facilities that need further evaluation because the facilities appear to have been closed, have an incorrect location, be a duplicate, not be a beverage bottling facility, not be a production location, and (or) have insufficient information to confirm facility existence (table 7). Of these, 175 facilities were removed during the inventory review and quality assurance checks, leaving another 421 that need further evaluation. These 421 facilities had the following statuses: (1) closed-confirmed, 34 facilities; (2) closed-unconfirmed, 11 facilities; (3) active-confirmed, 27 facilities; and (4) active-unconfirmed, 349 facilities. Possible actions for these facilities would include (1) facilities that have closed would be left in the inventory and their status updated, (2) facilities with no information available through online and mapping searches might be removed or have their status updated, (3) duplicates would be removed, (4) facilities with an incorrect location would be evaluated to ensure there was an entry in the inventory for the facility at the correct location or the facility record would be revised to the correct location, and (5) facilities that are not a beverage manufacturing location would be removed. In both assessments, the largest number of bottled water and breweries had inaccurate information, such as business classification (for example, NAICS codes) or location, from available data sources and may need to be removed or updated.
The Great Lakes regional assessment identified 288 facilities that had been missed and need to be added to the inventory (table 8). Of these, 124 were added during the national review, leaving 164 newly identified facilities to be added to the inventory in version 2. In both assessments, most of the facilities added were wineries. No soft drink or ice manufacturing facilities were identified to be added and only two bottled water facilities were determined to be missing from the inventory. This difference may be explained by individual bottled water and soft drink facility information being more difficult to find online because these businesses are often part of national chains, or the website presence for small individual facilities seems to be hard to find or nonexistent. In contrast, breweries, wineries, and distilleries are more often individual locations with more prevalent advertising online.
Table 7.
Count and percent of facilities identified during Great Lakes assessment that have been or may need to be removed from the inventory.[ --, no data]
Table 8.
Count and percent of facilities identified during Great Lakes assessment that have been or may need to be added to the inventory.[ --, no data]
This independent assessment of the inventory in the Great Lakes region confirmed the difficulty in finding accurate and complete facility information in the absence of a publicly available national list. The source of water required manual searches of facility web pages and was often not indicated. Overall, the Great Lakes assessment method and the national inventory GIS method determined the same source of water for more than 57 percent (83 of 145) of facilities. Comparison of water sources used by other nearby facilities may lead to inaccurate conclusions, especially in cases where the source of water is located some distance from or is transported to the production facility. Some data sources do not have current facility information owing to incomplete or inaccurate facility reporting, facility openings and closings, or data-entry errors. The national inventory work removed almost 30 percent of incorrect sites identified during the Great Lakes assessment. Some of the remaining sites identified for removal may stay in the inventory with an updated status of active-unconfirmed or closed-confirmed. The national inventory work identified about 43 percent of the new sites to add that were found during the Great Lakes assessment. Most of the remaining ones to add are wineries, which were not the primary focus of the national inventory effort. Only two bottled water facilities were determined to be missing in the Great Lakes region, indicating that the effort to include these facilities was largely successful.
Summary
The U.S. Geological Survey developed a comprehensive national inventory of beverage bottling facilities, including locations, water sources, water use, and a collection of other attributes, as a basis for an assessment of potential effects of extraction of water for bottling. Development of a national list was needed to determine where water was likely to be withdrawn for beverage bottling operations. Beverage types in subsector 312 (Beverage and Tobacco Product Manufacturing) were compiled for this effort and included facilities with the following North American Industrial Classification System codes as a primary or secondary classification type: (1) 312111, soft drink manufacturing; (2) 312112, bottled water manufacturing; (3) 312113, ice manufacturing; (4) 312120, breweries; (5) 312130, wineries; and (6) 312140, distilleries.
Available information was compiled for 43,365 facilities from multiple sources; however, water-use data could only be acquired for 257 (0.6 percent) facilities. Source of water was estimated for 41,663 (96 percent) facilities. Ancillary facility attributes were available for some facilities from a proprietary business list, but attributes were not available for all facilities in the inventory. In the absence of a national list for comparison and with some information unobtainable, limitations and potential deficiencies need to be communicated to users of the inventory so that appropriate assessments can be done. To describe the data quality of the facility and water-use information in the inventory, the following data-quality aspects were used: (1) completeness, (2) uniqueness, (3) validity, (4) timeliness, (5) accuracy, (6) consistency, and (7) accessibility. Data-quality aspects apply to information in the inventory tables and to the process and challenges encountered while creating the inventory. This report identifies data and knowledge gaps of the facility and water-use tables and the potential implications of these data and knowledge gaps.
Incomplete data can compromise the validity and reliability of the data. Errors in facility counts could result in over- or underestimating the potential for hydrologic effects on water resources. The presence of duplicate facility listings could bias the number of beverage bottling operations and the assessment of potential effects of water extractions. Inaccuracies in facility attributes might lead to incorrect conclusions in cases where those attributes are used for other analyses. Potential locational issues or inaccuracies could propagate to other facility attributes, such as source of water. A concurrent evaluation of facilities in the Great Lakes region with an undetermined source of water further emphasized many of these issues. Some facilities were determined to be incorrectly located, duplicated, or missing from the inventory. Many of the issues identified during the Great Lakes regional assessment were incorporated in a version 2 of the inventory. Many records have an unconfirmed status as active or closed and would require additional work to verify facility status. Knowledge of active facilities would be needed to adequately assess potential effects and determine where withdrawals are occurring across the United States. Selection of all facilities for a given product type may be incorrect because the inventory may not represent all manufacturing locations. Attributes may represent multiple product lines with insufficient information to determine this information for the individual beverage types of interest. With inconsistent status and unverified facility attribute information, it may also be difficult to make appropriate analyses when all information is not representative of the same year. The absence of a source for a complete publicly available bottling facility inventory meant that potential effects of water extractions might be missed where facilities exist but were not captured in the inventory.
Determination of potential hydrologic effects depends on knowledge of withdrawal amounts and the source of water. Publicly available water-use data were sparse for all bottling types and unavailable for wineries. The source of water for facilities with water-use data was known for most of the withdrawals, and most facilities (54.1 percent) relied on self-supplied sources of water. However, close to a third (28.5 percent) relied on public-supply deliveries. Determining or acquiring the quantity of water delivered to bottling facilities from public-supply systems is difficult, making evaluation of potential hydrologic effects problematic because the withdrawals for bottling facilities are one part of total withdrawals by the public-supply water system. Water-use values included some information about how the amounts were determined; however, some are capacities or permitted values and do not represent actual withdrawals. Other values were estimated and may not represent actual withdrawal amounts. The amount of water-use data was very limited temporally and spatially. Limited temporal range in available water-use data will limit the ability of the data user to estimate trends in withdrawals and (or) may skew descriptive statistical reporting of estimated water withdrawals. Determining if and when a facility produced a product was difficult because this information was often not publicly available. Additionally, water-use amounts were provided for the facility and not by individual product line. Therefore, water-use amounts may not be consistent from facility to facility and conclusions for potential effects may be inaccurate or misleading. These water-use data may also not be representative of all facility types across the United States. Despite the aforementioned limitations, the facility and water-use tables provide the first ever publicly available inventory of beverage and ice manufacturing facilities across the United States. The facility locations and other ancillary attributes provide information useful for assessment of potential effects of water extractions. The potential data limitations and knowledge gaps are described in this report so that users of the data can make appropriate and relevant analyses.
References Cited
Beverage Marketing Corporation, 2023, Bottled water dubbed most popular beverage, despite slowed growth: Food & Beverage Insider, accessed July 1, 2024, at https://www.beveragemarketing.com/news-detail.asp?id=746.
Blue Triton, 2023, Blue Triton brands: Blue Triton web page, accessed December 6, 2023, at https://www.bluetritoncareers.com/our-brands/.
Buchwald, C.A., Houston, N.A., Stewart, J.S., York, B.C., and Valseth, K.J., 2022, Public-supply water service areas within the conterminous United States, 2017: U.S. Geological Survey data release, accessed May 3, 2022, at https://doi.org/10.5066/P9I22Z24.
Buchwald, C.A., Luukkonen, C.L., Martin, G.R., Kennedy, J.L., Wilson, J.T., Hian, M.E., and Dieter, C.A., 2023, Inventory of water bottling facilities in the United States, 2023, and select water-use data, 1955–2022: U.S. Geological Survey data release, accessed March 18, 2024, at https://doi.org/10.5066/P90Z125H.
Buchwald, C.A., Luukkonen, C.L., Martin, G.R., Johnson McKee, A.E., Kelley, R.L., and Dieter, C.A., 2024, Inventory of water bottling facilities in the United States, 2024, and select water-use data, 1955–2023 (version 2): U.S. Geological Survey data release, accessed November 2024 at https://doi.org/10.5066/P1WAH5Q8.
Data Axle, 2023, Data Axle business database: Data Axle web page, accessed May 5, 2023, at https://www.data-axle.com/what-we-do/reference-solutions.
Dun & Bradstreet, 2023, Beverage manufacturing companies in United States of America: Dun & Bradstreet webpage, accessed November 21, 2023, at https://www.dnb.com/business-directory/company-information.beverage_manufacturing.us.html.
Dun & Bradstreet, 2024, Business information report snapshot: Dun & Bradstreet web page, accessed February 20, 2024, at https://www.dnb.com/marketing/media/birsnapshot.html?utm_source=google&utm_medium=cpc&utm_campaign=BrandedCampaign&utm_content=&utm_term=&campaignid=1 8510109100&adgroupid=&creativeid=&gad_source=1&gclid=EAIaIQobChMI6s7w4fb7gwMVMS-tBh2B9wvsEAAYASAAEgKuT_D_BwE&gclsrc=aw.ds.
Homeland Security Information Network, 2016, Homeland Infrastructure Foundation-Level Data (HIFLD) secure and licensed food industry and manufacturing category shapefiles: Dun and Bradstreet Worldbase database, accessed November 7, 2019, at https://gii.dhs.gov/hifld/data/secure.
IBISWorld, Inc., 2021, Industry reports for soda, bottled water, breweries, wineries, and distilleries: IBISWorld, Inc., web page, accessed January 3, 2022, at https://www.ibisworld.com/.
International Packaged Ice Association, 2024, Find safe ice: International Packaged Ice Association web page, accessed July 10, 2024, at https://www.safeice.org/find-safe-ice.html.
Jordan, S., 2021, Online presence management tips for small businesses: Top Design Firms, Clutch, accessed February 20, 2024, at https://topdesignfirms.com/web-design/blog/online-presence-management.
Mergent, 2024, Mergent online: Mergent web page, accessed February 20, 2024, at https://www.mergentonline.com/login.php.
NAICS Association, 2023, NAICS codes that fall under 3121—Beverage manufacturing: NAICS Association web page, accessed November 17, 2023, at https://www.naics.com/naics-code-description/?code=3121#:~:text=This%20industry%20group%20comprises%20establishments%20primarily%20engaged%20in,Codes% 20that%20fall%20under%203121%20-%20Beverage%20Manufacturing.
Olson, D., 2022, Why some small businesses don’t use websites: Martech Series, accessed February 20, 2024, at https://martechseries.com/mts-insights/guest-authors/why-some-small-businesses-dont-use-websites/.
Primo water, 2021, Primo water refill stations: Primo water web page, accessed June 2021, at https://primowater.com/self-service-refill-water/.
Rdocumentation, 2023, stringdist-metrics—String metrics in stringdist: Stringdist (version 0.9.12), accessed December 11, 2023, at https://www.rdocumentation.org/packages/stringdist/versions/0.9.12/topics/stringdist-metrics.
Reddy Ice, 2022, Reddy Ice location search and directory: Reddy Ice web page, accessed October 31, 2022, at https://www.reddyice.com/locations.
U.S. Census Bureau, 2021, County business patterns: Complete United States File, accessed November 17, 2023, at https://www.census.gov/data/datasets/2021/econ/cbp/2021-cbp.html.
U.S. Congress, 2021, Department of the Interior, Environment, and related agencies appropriations bill: 116th Congress 2nd Session, House of Representatives, Report 116–448, 255 p., accessed January 15, 2024, at https://www.congress.gov/116/crpt/hrpt448/CRPT-116hrpt448.pdf.
U.S. Congress, 2022, Department of the Interior, Environment, and related agencies appropriations bill: 117th Congress 1st Session, House of Representatives, Report 117–83, 313 p., accessed January 15, 2024, at https://www.congress.gov/117/crpt/hrpt83/CRPT-117hrpt83.pdf.
U.S. Environmental Protection Agency, 2023, Safe drinking water information system (SDWIS) Federal reporting services: U.S. Environmental Protection Agency web page, accessed November 22, 2023, at https://www.epa.gov/ground-water-and-drinking-water/safe-drinking-water-information-system-sdwis-federal-reporting.
U.S. Food and Drug Administration, 2022, Bottled water everywhere—Keeping it safe:, U.S. Food and Drug Administration web page, accessed December 2022 at https://www.fda.gov/consumers/consumer-updates/bottled-water-everywhere-keeping-it-safe.
U.S. Food and Drug Administration, 2023, 165.110 Bottled water: U.S. Food and Drug Administration web page, accessed December 4, 2023, at https://www.ecfr.gov/current/title-21/chapter-I/subchapter-B/part-165/subpart-B/section-165.110.
U.S. Geological Survey, 2024, Hydrologic unit maps: U.S. Geological Survey web page, accessed February 2, 2024, at https://water.usgs.gov/GIS/huc.html.
VinePair, Inc., 2023, The States with the most wineries in 2021: accessed November 29, 2023, at https://vinepair.com/articles/map-states-wineries/.
Watermill Express, 2021, Watermill express, pure drinking water and ice: Watermill Express web page, accessed June 2021 at https://watermillexpress.com/.
Glossary
Bottled water
Water that is intended for human consumption and that is sealed in bottles or other containers with no added ingredients, except that it may contain safe and suitable antimicrobial agents. Bottled water is regulated under the U.S. Food and Drug Administration (U.S. Food and Drug Administration, 2022). Facilities are classified under the North American Industrial Classification System with code 312112 for bottled water manufacturing.
Breweries
Establishments primarily engaged in brewing beer, ale, lager, malt liquors, kombucha, and nonalcoholic beer. Facilities are classified under the North American Industrial Classification System with code 312120 for breweries.
Distilleries
Establishments primarily engaged in one or more of the following: distilling potable liquor (except brandies), distilling and blending liquors, and blending and mixing liquors and other ingredients. Facilities are classified under the North American Industrial Classification System with code 312140 for distilleries.
Drinking water
Different types of drinking water include municipal/tap, mineral, distilled, purified, alkaline, natural spring, infused, and sparkling.
Soft drinks
Similar to bottled water and may or may not have carbonation, including soda water, tonic water, and seltzer. This type of beverage is based on a North American Industrial Classification System code 312111 and as such includes noncarbonated beverages of iced coffee, iced tea, flavored water, fizzy water, and fruit drinks (except juice itself). Soft drinks are regulated by the U.S. Food and Drug Administration under different regulations than bottled water (U.S. Food and Drug Administration, 2022).
Sparkling bottled water
Water that, after treatment and possible replacement of carbon dioxide, contains the same amount of carbon dioxide that it had at emergence from the source.
Spring water
Water derived from an underground formation from which water flows naturally to the surface of the Earth, which is collected only at the spring or through a bore hole tapping the underground formation feeding the spring (U.S. Food and Drug Administration, 2023, 21 Code of Federal Regulations 165.110).
Water bottling facility
A place of manufacturing where the facility bottles water or other beverages containing water, or manufactures ice. These facilities are classified under the North American Industrial Classification System subsector code of 312 for Beverage and Tobacco Product Manufacturing. The beverage types compiled for this effort include facilities with the following North American Industrial Classification System codes as a primary or secondary classification type: (1) 312111: Soft drink manufacturing, (2) 312112: Bottled water manufacturing, (3) 312113: Ice manufacturing, (4) 312120: Breweries, (5) 312130: Wineries, and (6) 312140: Distilleries.
Wineries
Establishments primarily engaged in one or more of the following: growing grapes and manufacturing wines and brandies, manufacturing wines and brandies from grapes and other fruits grown elsewhere, and blending wines and brandies. Facilities are classified under the North American Industrial Classification System with code 312130 for wineries.
For more information about this publication, contact:
Director, USGS Upper Midwest Water Science Center
2280 Woodale Drive
Mounds View, MN 55112
763–783–3100
For additional information, visit: https://www.usgs.gov/centers/umidwater
Publishing support provided by the
Rolla Publishing Service Center
Disclaimers
Any use of trade, firm, or product names is for descriptive purposes only and does not imply endorsement by the U.S. Government.
Although this information product, for the most part, is in the public domain, it also may contain copyrighted materials as noted in the text. Permission to reproduce copyrighted items must be secured from the copyright owner.
Suggested Citation
Luukkonen, C.L., Buchwald, C.A., Martin, G.R., and Johnson Mckee, A.E., 2024, Data and knowledge gaps of a water bottling facility inventory and select water-use dataset, United States: U.S. Geological Survey Scientific Investigations Report 2024–5106, 41 p., https://doi.org/10.3133/sir20245106.
ISSN: 2328-0328 (online)
Study Area
Publication type | Report |
---|---|
Publication Subtype | USGS Numbered Series |
Title | Data and knowledge gaps of a water bottling facility inventory and select water-use dataset, United States |
Series title | Scientific Investigations Report |
Series number | 2024-5106 |
DOI | 10.3133/sir20245106 |
Year Published | 2024 |
Language | English |
Publisher | U.S. Geological Survey |
Publisher location | Reston, VA |
Contributing office(s) | Upper Midwest Water Science Center |
Description | Report: vi, 41 p.; 2 Data Releases |
Country | United States |
Online Only (Y/N) | Y |
Additional Online Files (Y/N) | N |