Temperature
Links
- Document: Report (940 KB pdf) , HTML , XML
- Related Work: Techniques and Methods 9-A0 - General introduction for the “National Field Manual for the Collection of Water-Quality Data”
- Project Site: National Field Manual for the Collection of Water-Quality Data (NFM)
- Superseded Publications:
- Download citation as: RIS | Dublin Core
Abstract
The “National Field Manual for the Collection of Water-Quality Data” (NFM) provides guidelines and procedures for U.S. Geological Survey (USGS) personnel who collect data used to assess the quality of the Nation’s surface-water and groundwater resources. This chapter, NFM A6.1, provides guidance and protocols for the measurement of temperature of air, of a surface-water body or in groundwater, which include the scientific basis of the measurement, selection and maintenance of equipment, calibration verification, troubleshooting, and procedures for measurement and reporting. It updates and supersedes USGS Techniques of Water-Resources Investigations, book 9, chapter A6.1, version 2.0, by Franceska D. Wilde.
Temperature of air and water is routinely measured when water samples are collected, is often measured continually at USGS streamgages, and is a parameter regularly measured during laboratory and field experiments. The field method for measuring temperature described in this chapter is applicable to air and most natural waters.
Before 2017, the NFM chapters were released in the USGS Techniques of Water-Resources Investigations series. Effective in 2018, new and revised NFM chapters are being released in the USGS Techniques and Methods series; this series change does not affect the content and format of the NFM. More information is in the general introduction to the NFM (USGS Techniques and Methods, book 9, chapter A0) at https://doi.org/10.3133/tm9A0. The authoritative current versions of NFM chapters are available in the USGS Publications Warehouse at https://pubs.usgs.gov. Comments, questions, and suggestions related to the NFM can be addressed to nfm@usgs.gov.
1.0. Introduction
The “National Field Manual for the Collection of Water-Quality Data” (NFM) is the official and citable protocol for the collection of water-quality data by the Water Mission Area (WMA) of the U.S. Geological Survey (USGS). The NFM provides guidelines and procedures for USGS personnel who collect data for water quality in surface water and groundwater, with detailed, comprehensive, and citable procedures.
National USGS program and project personnel, as well as those in USGS Water Science Centers collecting water-quality data, for projects supported by USGS Cooperative Matching Funds, are mandated to use protocols provided in the NFM (USGS Office of Water-Quality Technical Memorandum 2002.13—U.S. Geological Survey, 2002). Formal training, as provided in the USGS class “Field Water-Quality Methods for Groundwater and Surface Water,” and field apprenticeships supplement the information provided in the NFM and support the collection of unbiased, high-quality data.
The USGS National Field Manual provides detailed, comprehensive, and citable procedures for monitoring the quality of surface water and groundwater. Formal training and field apprenticeships supplement the information provided in the NFM.
Chapter A6.1 provides guidance and protocols for the measurement of temperature of air, of a surface-water body or in groundwater, which include the scientific basis of the measurement, selection and maintenance of equipment, calibration verification, troubleshooting, and procedures for measurement and reporting. Temperature is an important variable in aquatic systems, and accurate measurements of this property are the basis for describing other attributes of those systems. Temperature is routinely measured when water samples are collected, is often measured continually at USGS streamgages, and is regularly measured during laboratory and field experiments.
This chapter updates and supersedes USGS Techniques of Water-Resources Investigations, book 9, chapter A6.1, version 2.0 (Wilde, 2006). It covers the physical basis for measurement of temperature in aqueous solutions, as well as factors that affect the measurement, terminology, method protocols, and applications. The field method described in this chapter is applicable to air and most natural waters.
Before 2017, the USGS NFM chapters were released in the USGS Techniques of Water-Resources Investigations series. Effective in 2018, new and revised NFM chapters are being released in the USGS Techniques and Methods series; this series change does not affect the content and format of the NFM. More information is in the general introduction to the NFM (USGS Techniques and Methods, book 9, chapter A0—U.S. Geological Survey, 2018) at https://doi.org/10.3133/tm9A0. The authoritative current versions of NFM chapters are available in the USGS Publications Warehouse at https://pubs.usgs.gov. Comments, questions, and suggestions related to the NFM can be addressed to nfm@usgs.gov.
1.1. Overview of Temperature
Measurements of air and water temperature at a field site are essential for water-quality data collection. Determination of dissolved-oxygen concentrations, conductivity, pH, rate and equilibria of chemical reactions, biological activity, and fluid properties relies on accurate temperature measurements. The USGS currently (2024) measures and publishes water temperature data at more than 3,500 surface-water and groundwater stations, including wells, springs, streams, lakes, rivers, estuaries, and marine environments (U.S. Geological Survey, undated). Water temperature data are provided to cooperators, data managers, scientists, and the public. Water temperature is often measured in conjunction with other water-quality parameters to support habitat assessment of threatened and endangered species and to evaluate changing climate conditions. Accurate air- and water-temperature data are essential to document thermal alterations to the environment caused by natural phenomena and by human activities. Water temperature can be subject to environmental regulation and monitoring by State and local agencies.
2.0. Equipment and Supplies
A temperature sensor is any device used to measure temperature. In its simplest form, a temperature sensor can contain a detector that creates a signal used to infer temperature according to a calibration. Standard procedures used in the past by the USGS to measure temperature involved the use of liquid-in-glass thermometers. Since the 1990s, digital thermometers and other equipment utilizing integrated thermistors and thermocouples, such as multiparameter instruments, have continued to undergo improvements in accuracy, reliability, and cost. Digital thermometers have many advantages over liquid-in-glass thermometers, including smaller uncertainties, faster response, ease of automation, and elimination of uncertainty related to lighting and viewing angle (Ripple and Strouse, 2005). Electronic temperature sensors vary voltage, resistance, current, or frequency outputs with temperature. Common sensors include thermistors, an electrical resistor with a resistance that varies sharply and predictably with temperature, and thermocouples, sensors containing two dissimilar metals bonded to form a connection with a dielectric potential that varies with temperature. To make a digital thermometer, a sensor—either thermistor or thermocouple—is connected to a signal conditioning device which linearizes the signal that communicates information to a display.
Digital thermometers and multiparameter instruments utilizing integrated sensors have replaced liquid-in-glass thermometers for nearly all USGS temperature measurements. Barring any project-specific requirements, using digital thermometers or equipment utilizing integrated sensors, such as multiparameter instruments, should be considered the standard field method for temperature measurement of water and air. Liquid-in-glass thermometers containing mercury must never be taken to the field (USGS Office of Water-Quality Technical Memorandum 1994.02—U.S. Geological Survey, 1993). Mercury is a hazardous substance, and its use should be avoided to prevent contamination and danger to personnel. Mercury-filled and liquid-in-glass thermometers in general should be phased out using digital thermometers and other equipment utilizing integrated sensors whenever possible.
Other types of sensors for temperature measurement include fiber-optic sensors and infrared (IR) thermometers. These systems are generally applied to situations where heat flow is occurring in a medium or temperature is used to trace mass flux. Fiber-optic temperature sensors contain a light source and detector. These sensors work by detecting changes in the wavelength of light caused by temperature. Fiber-optic sensors can be useful for measuring distributed temperatures across multiple locations along a fiber-optic strand and relative temperature differences. Infrared thermometers and temperature sensors work by focusing the temperature-dependent IR radiation emitted from an object onto a detector and converting the energy into a measurable electrical signal. The construction of the focusing and detecting elements of an IR thermometer determines its range and accuracy. Forward-looking infrared (FLIR) thermometers combine an IR temperature sensor with camera technology to produce an image or a movie of temperatures depicted by a scale of colors. Depending on the processor, focusing method, and detector used, FLIR thermometers can produce high-resolution temperature images and are powerful tools for determining relative temperature differences.
Infrared thermometers (including FLIR) detect surface temperature only and can be used for groundwater/surface-water interaction studies or other hydrologic applications where information about surface temperature variation is useful. Their accuracy is limited due to reflections of IR sources off the water surface and movement of the water itself, making them undesirable for routine water temperature measurement. Procedures for the use of fiber-optic, IR, and other non-contact methods of measuring temperature are beyond the scope of this NFM chapter. Quality assurance (QA) procedures for these and other sensor types is left up to the users and is determined by the specific project objectives.
Where applicable, temperature-measurement equipment and supplies (described in box 6.1-1) must be tested before temperature data are collected and cleaned soon after use. Each thermometer or sensor must have a logbook in which all calibrations and repairs are recorded, along with the manufacturer make and model and serial number. Logbooks may be in digital or paper form. A sensor should have its own logbook if calibration information is stored in the sensor or a digital thermometer may have a logbook if the thermometer electronics and sensor are calibrated as a unit as in the case of many digital thermometers.
-
➢ This chapter covers measurement and QA procedures for digital thermometers and other equipment utilizing integrated thermistors and thermocouples. Liquid-in-glass thermometers should be phased out.
-
➢ Procedures for the use of fiber-optic, IR, and other non-contact methods of measuring temperature are beyond the scope of this NFM chapter.
-
➢ All temperature sensors collecting data for publication by the USGS are required to undergo the QA verification procedures described in this chapter or a similar QA verification process if the procedures described in this chapter do not fit the technology.
Box 6.1. -1. Equipment and supplies used for measuring temperature
Modify this list to meet the specific needs of the field effort.
-
✓ Certified digital thermometer or sensor which must carry a current certificate of calibration.
-
✓ Sensor to classify as traceable for providing traceability to field measurements.
-
• Temperature range, at least –5 to 45°C
-
• Required accuracy of less than or equal to ±0.2°C
-
• Required to be compared directly to a certified sensor having a valid certificate, using a refrigerated water bath, at no less than five points, between 0 and 40°C, annually and at two points bracketing the expected range of use no more than 6 months from the five-point comparison. Each point in the comparison is required to agree with the certified sensor by less than or equal to ±0.2°C.
-
-
✓ Verified temperature sensor for data collection and publication.
-
• If the sensor data are used to correct another water-quality parameter, the accuracy of the sensor is required to be less than or equal to ±0.2°C.
-
• If the sensor data are NOT used to correct another water-quality parameter, the accuracy of the sensor is determined by project objectives.
-
• Required to be compared against and verified with a traceable or certified sensor at points across the range of use, annually, to define and verify uncertainty. The verification procedure is outlined in section 3.0 Calibration Verification.
-
✓ Dewar flask and (or) plastic beakers (assorted sizes)
-
-
✓ Refrigerated water bath
-
✓ Soap solution, 0.1–0.2%, non-phosphate laboratory detergent
-
✓ Deionized water (1 liter), ASTM type 2 or better
-
✓ Flowthrough chamber (for groundwater applications as an alternative to multiparameter instruments with downhole capabilities)
-
✓ Paper tissues, disposable, soft, and lint-free
-
✓ Logbook, for recording all calibrations, maintenance, and repairs, may be digital or paper
2.1. Definitions
Within this chapter the following terms will be used and are defined as follows:
-
Certified Temperature Sensor.— A sensor with a valid calibration certificate of NIST traceability from a laboratory certified by NIST's National Voluntary Laboratory Accreditation Program (NVLAP) (NIST, 2024). For use in the procedures outlined in this chapter, these sensors or digital thermometers are required to have a range of at least -5°C to 45°C, and a certified accuracy of less than or equal to ±0.05°C with a readout resolution of at least 0.001°C. The calibration certificate is valid for up to 2 years.
-
Traceability.— Property of a result of a measurement or value of a standard whereby it can be related with a stated uncertainty, to stated references, usually national or international standards, through an unbroken chain of comparisons (NIST, 2023).
-
Traceable Temperature Sensor.— A sensor that is compared to a certified sensor every 6 months in an unbroken chain of comparison measurements that lead back to NIST standards through a certified sensor. It has a range of at least -5°C to 45°C and a manufacturer’s stated accuracy of less than or equal to ±0.2°C. Section 2.2 Establishing and Maintaining a Traceable Sensor outlines the procedure required to establish the chain of comparisons, which are made with a certified sensor. Traceable sensors are used for discrete data collection and as a reference sensor to verify the accuracy of deployed sensors.
-
Verified Temperature Sensor.— A sensor with documented data quality determined via an annual comparison to a traceable or certified temperature sensor, creating NIST traceability. Uncertainty in a sensor's measurements increases with each additional degree of separation from a certified standard. Therefore, the sensor is required to go through procedures described in section 3.0 Calibration Verification to define and verify the uncertainty of data collected with a sensor and establish traceability, regardless of the sensor's accuracy requirement. Verified sensors may be used for continuous temperature measurements and data collection for publication. An accuracy specification for a verified sensor is only required if the sensor is bundled onto a multiparameter instrument and is used to correct another water-quality parameter (such as dissolved oxygen or specific conductance). The accuracy of such a sensor is required to be less than or equal to ±0.2°C.
-
Water Temperature Sensor.—Any integrated sensor or technology used to measure water temperature utilizing a thermistor or thermocouple. This can be a sensor combined with a readout device to form a digital thermometer or a multiparameter instrument with an integrated temperature sensor.
The relation of the sensor classifications defined above can be seen in figure 6.1-1. The procedures in this chapter should provide traceability of all temperature measurements to certified sensors.
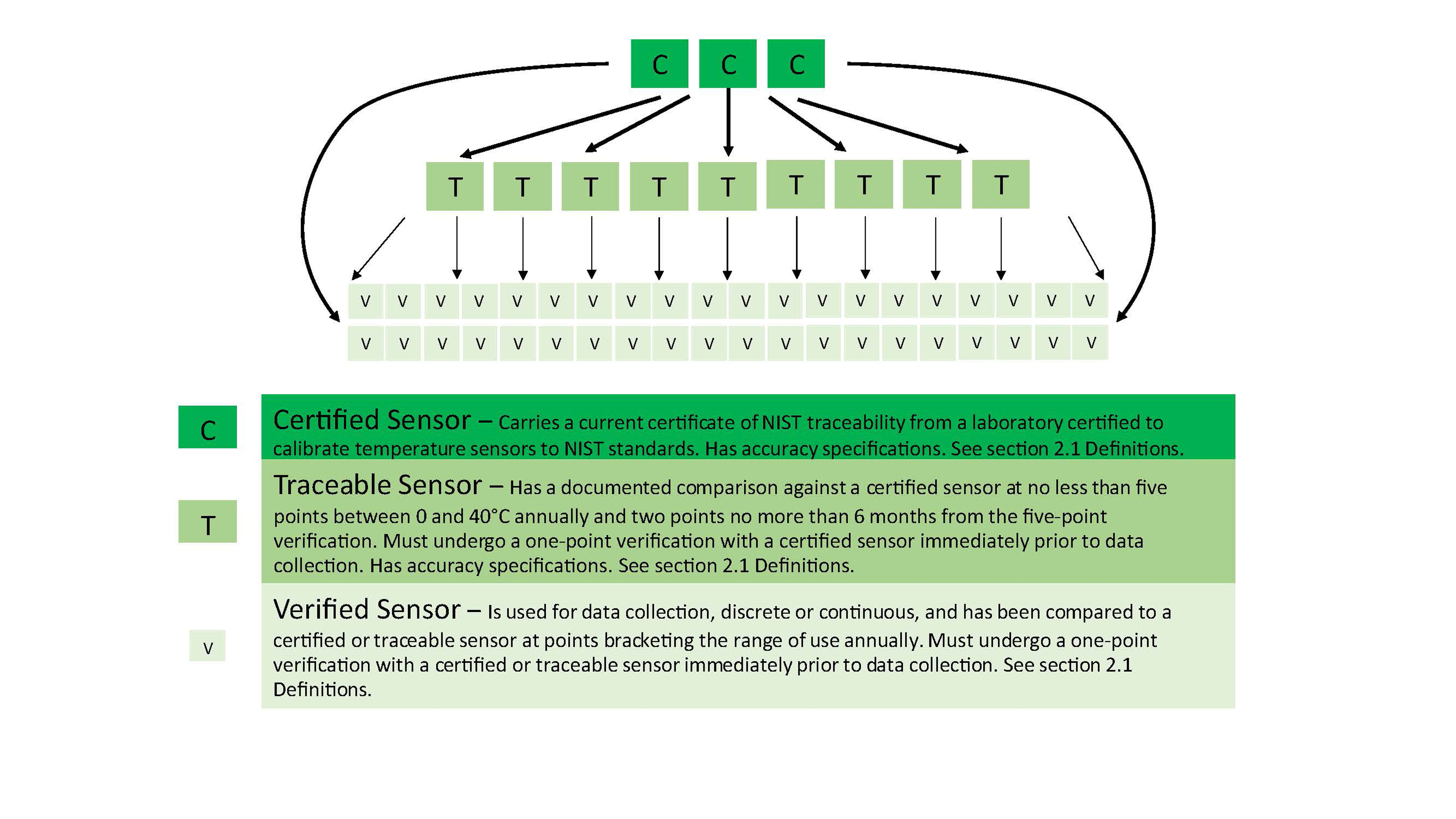
-1. Relations of the sensor types defined in section 2.1.
2.2. Establishing and Maintaining a Traceable Sensor
To maintain rigorous traceability, a sensor classified as traceable is required to be compared with a certified sensor or digital thermometer at no less than five points between 0°C and 40°C annually. Additionally, a traceable sensor is required to be compared against a certified sensor no more than 6 months from the five-point comparison at two points which bracket the range of use during the period. Traceable sensors may be used to verify calibrations of sensors used to collect data and (or) to actually collect data. Any sensor that meets the minimum requirements for accuracy and resolution (defined in section 2.1) may be classified as traceable so long as the procedure in this section is completed. If the expected range of use is greater than 40°C, additional comparison points are required. All comparison points must agree within ±0.2°C. All temperature comparisons or verifications are to be documented in the calibration and maintenance log. A refrigerated water bath is necessary for establishing and maintaining a traceable sensor.
-
1. Immerse the traceable and certified sensors in the refrigerated bath with a water temperature of approximately 0°C. Be sure the temperature of the water bath is equilibrated and stable. There should be no positive or negative trends in temperature readings taken from the water bath with the certified sensor.
-
2. Position the sensors next to each other as close as possible (without contacting each other) and completely immersed. Stir or circulate the water bath and allow at least 2 minutes for the temperature to stabilize.
-
3. Without removing the sensors from the refrigerated water bath, record the sensor measurements to the nearest 0.01°C or the maximum resolution of the displays.
-
4. Record three measurements at least 1 minute apart from each other within a 5-minute span for each sensor.
-
5. Calculate the mean of the three temperature measurements for each sensor then compare the mean value of the traceable sensor with the certified sensor.
-
6. Repeat steps 1–5 in 15°C, 25°C, 30°C, and 40°C water baths.
-
7. Identify sensors that are within ±0.2°C of the certified sensor for all points checked as “traceable” with the verification date, and certifier’s initials. If a sensor does not check to within ±0.2°C of the certified sensor for all points checked, it cannot be labeled and used as a traceable sensor. Verify traceable sensors at a minimum of every 6 months. Document the results in the calibration and maintenance logbook or electronic log.
2.3. Maintenance, Cleaning, and Storage
Digital thermometers and temperature sensors need proper maintenance, storage, and cleaning procedures to prevent them from becoming damaged or otherwise out of calibration. Digital thermometers can become damaged by excessive heat, cold, vibration, shock, cable and connection damage, and water intrusion into the readout case. Many digital thermometers are not water resistant or waterproof. The ends of some cabled sensors may not be waterproof or intended for complete immersion. Most certified digital thermometers are certified as a unit containing the sensor and readout device together. Replacing one or the other component may negate the certification, requiring recertification. It is important to be familiar with and to follow the manufacturer’s instructions for use and care.
-
➢ Check manufacturer’s instructions for the temperature sensor’s depth limit, if it has one, and compatibility with corrosive solutions. Avoid submerging the sensor past its depth limit or in corrosive solutions unless compatibility is confirmed by the manufacturer.
-
➢ Digital thermometers should not be submerged in water unless the manufacturer affirms that they are waterproof. Do not allow any liquid to enter open jacks that are part of some digital thermometers.
-
➢ Keep thermometers clean.
-
• Clean thermometer sensors with a soft cloth dipped in a mild solution of warm water and non-phosphate detergent.
-
• If the digital thermometer sensor and case needs to be disinfected, use a weak (0.005 percent) bleach solution or a wipe containing bleach.
-
• Do not autoclave temperature sensors (unless autoclaving is sanctioned by the manufacturer).
-
• If your digital thermometer has a detachable sensor with a plug termination, periodically wipe off or clean the sensor contacts. Dirty, loose, or corroded contacts can affect temperature readings.
-
• Blot the thermometer sensor dry after use.
-
-
➢ Store digital thermometers securely when not in use.
-
• Keep digital thermometers in a protective case stored in a clean, dry, climate-controlled area when not in use. Each thermometer sensor and case must be free of sand and debris. Avoid storage in vehicles.
-
• Keep digital thermometers dry and in a protective case during transit to prevent excessive vibration.
-
• Check the batteries of digital thermometers for proper voltage and replace regularly. Be sure the battery compartment is clean and dry.
-
A separate logbook or electronic log for recording repair, maintenance, and calibration history information is required to be maintained for each piece of field equipment or replaceable sensor that stores calibration information within the sensor’s internal processor. The logbook should travel with the equipment or be accessible through electronic means. The pages of a paper logbook should be prenumbered consecutively. Do not skip or tear out pages. Water-resistant paper is recommended. Paper logbooks are available to USGS personnel only through One-Stop shopping (https://1stop.usgs.gov/; item Q609FLD).
USGS personnel are encouraged to use electronic rather than paper field notes to increase efficiency and minimize transcription errors. Office of Water Quality Technical Memorandum 2016.09 (U.S. Geological Survey, 2016) recommends that all water-quality records, including logbooks, be collected electronically wherever feasible and specifies requirements for electronic records.
3.0. Calibration Verification of Temperature Sensors
Temperature sensor and digital thermometer calibration differ from the process by which a pH or conductivity sensor is adjusted until the accuracy of its performance conforms to that of an accepted calibration standard. For temperature sensors, calibration refers to a verification of calibrated accuracy at a range of temperatures covering the expected or actual range of use or deployment. The verification comparison is done with a certified or traceable thermometer or sensor. A traceable classification for a temperature sensor can be accomplished by following the procedures in section 2.2 Establishing and Maintaining a Traceable Sensor. A new sensor is required to be checked against a certified or traceable sensor at points covering the range of expected temperature measurements using a water bath, before the sensor is used to collect environmental data. Calibration verification of sensors collecting data for USGS publication is required to be performed every 12 months through one of the following two methods. Both methods are acceptable and neither method is preferred.
Method 1.—The annual, required, verification is performed in a laboratory setting using a water bath by comparison with a certified or traceable sensor as described in section 3.2 Calibration Verification in a Laboratory Using a Water Bath. The water temperature range for verifications must bracket and include points that represent the range expected to be measured in the field. See section 3.1 Determination of Points for Sensor Calibration Verification to determine the range and number of verification points.
Method 2.— The annual verification requirement for deployed temperature sensors is met by performing a verification during each site visit throughout the year or field deployment period by comparison with a certified or traceable temperature sensor, in situ, and is an ongoing process for the annual temperature cycle. If this option is chosen, consult section 2.2 Establishing and Maintaining a Traceable Sensor and section 3.3 In Situ Calibration Verification of Sensors. Many traceable sensors may be established for use in calibration verifications. In situ verifications must be within the range of ambient temperatures for the site. See section 3.1 Determination of Points for Sensor Calibration Verification to determine the range and number of verification points. The methods and results of the sensor verification process must be documented and readily available.
In addition to the requirements for annual calibration verification, if a traceable or verified sensor is used to collect data, it must be checked against a certified sensor at one point, immediately before the field trip. This 1-point comparison can be done during calibrations of other sensors or as a stand-alone comparison.
Sensor verifications must be documented in the sensor logbook be it paper or electronic and may be duplicated with the data in a database or data release. Verification documentation is required to include the make, model, serial number, and verification water temperature measurements from the verified sensor and certified or traceable sensor.
3.1. Determination of Points for Sensor Calibration Verification
The points chosen for calibration verification are required to cover the range of expected or actual measurements. For verification of a new sensor, the requirements for the range and number of points chosen are the same as for annual calibration verification, however the range of expected temperature measurements must be known in order to satisfy the requirements. If the range of expected measurements is not known, the full range of the sensor (0–40°C) should be checked to ensure the calibration verification is sufficient to provide traceability of the measurements through the entire range eventually measured.
The minimum number of verification points is two. The verification points must be ±2°C of the minimum and maximum and ±4°C of the mean of the annual range. The verification points must be at least 2°C apart for sensors measuring small annual ranges. The points should be no more than ±4°C apart unless the sensor measures or will measure large annual ranges. For such sensors, verification points could be as much as ±10°C apart. The maximum number of points required is five. Quarterly checks of deployed sensors should satisfy the requirements for range and number of verification points.
The following are examples that show how to determine the minimum number of acceptable points for verifying temperature sensors for three annual ranges. These examples are idealized and simplified. All possible annual ranges cannot be covered by them. Consult a water-quality specialist if the site to be measured falls outside of the requirements or you are unsure how to determine the points for calibration verification.
-
• If the annual range of measurements at a site is 4°C and 12°C, the mean is 8°C. Two points verified at 6°C and 10°C satisfy the requirements because those points are ±2°C of the maximum and minimum and within ±4°C of the mean of the annual range. Because they are 4°C apart, the points satisfy the requirement that they be at least 2°C apart.
-
• If the annual range of measurements at a site is 2°C and 14°C, the mean is 8°C. Points verified at 4°C, 8°C and 12°C satisfy the requirements because those points are ±2°C of the minimum and maximum, are ±4°C of the mean, and are ± 4°C of each other.
-
• If the annual range of measurements at a site is 6°C and 38°C, the mean is 22°C and the range of measurement is 32°C. The maximum number of points required is five. Points verified at 8°C, 18°C, 26°C, 30°C, and 36°C satisfy the requirements because those points are ±2°C of the minimum and maximum, are ±4°C of the mean, are no more than 10°C apart, and are equally spaced about the range to provide no more than five total points. Note that this example provides an especially wide range of measurement for an annual period.
3.2. Calibration Verification in a Laboratory Using a Water Bath
This procedure is for calibration verification of sensors when equipment is removed from service and taken to a laboratory away from the field site. Note that if only a couple of points are necessary for verification, the in situ procedure using a traceable sensor (section 3.3 In Situ Calibration Verification of Sensors) may be a better option.
3.2.1. Calibration Verification Using a Refrigerated Water Bath
-
1. Immerse the sensors to be verified and the certified or traceable sensor in a refrigerated bath with water close to the temperature of the first verification point determined using the procedure outlined in section 3.1 Determination of Points for Sensor Calibration Verification. Be sure the temperature of the water bath is equilibrated and stable. There should be no positive or negative trends in temperature readings taken from the water bath with the certified or traceable sensor.
-
2. Position the sensors next to each other as close as possible (without contacting each other) and completely immersed. Stir or circulate the water bath and allow at least 2 minutes for the temperature to stabilize.
-
3. Without removing the sensors from the refrigerated water bath, record the sensor measurements to the nearest 0.01°C or the maximum resolution of the displays.
-
4. Record three measurements at least 1 minute apart from each other within a 5-minute span for each sensor.
-
5. Calculate the mean of the three temperature measurements for each tested sensor then compare the mean value with the certified or traceable sensor.
-
6. Repeat steps 1–5 for the other points to be verified
-
7. Identify sensors’ accuracy with difference in reference to the certified or traceable sensor with verification date, accuracy of the sensor, and certifier’s initials. Verify sensors for field data collection at least once every 12 months. Document the results in the calibration and maintenance logbook or electronic log.
3.2.2. Calibration Verification When a Refrigerated Water Bath is Not Available
This procedure is limited to points of 0°C (ice and deionized water [DIW] bath), room temperature (20–25°C), and points above room temperature using a circulated heated water bath. If the sensor to be verified is used mainly in a range between 0°C and 25°C, checking in a laboratory without a refrigerated water bath will not be adequate to represent the range of expected use. It will be necessary to use the in situ temperature verification procedures in section 3.3 In Situ Calibration Verification of Sensors.
3.2.2.1. Calibration Verification at 0°C
For a verification at a true reading of 0°C, it is necessary to use ice made with DIW in a bath of DIW. If a verification at a temperature near but not at 0°C is required, ice made with DIW in a bath of DIW is not required. Ice made with tap water in a bath of tap water may be substituted.
-
1. Freeze several ice cube trays filled with DIW. Access to an ice machine connected to a DIW water supply will be helpful for checking large equipment.
-
2. Fill a container of suitable size for the sensor verification about three-quarters full of deionized ice. The verification container can be as small as a 1,000-milliliter Dewar flask or larger if needed. Add chilled DIW to the container to nearly full capacity allowing room for displacement of the equipment to be verified. If using a smaller size container, it may be helpful to place the container of ice-DIW mixture in a larger, insulated container such as a cooler.
-
3. Completely immerse the certified or traceable sensor in the ice-DIW mixture. Make sure the temperature is uniform by stirring the mixture and checking at several locations within the bath with the certified or traceable sensor. Do not use the sensor to stir the bath. There should be no positive or negative trends in temperature readings taken from the water bath with the certified or traceable sensor. If there are trends in the readings or the bath temperature is not uniform, it may be necessary to stir more, add more ice, insulate the bath, or relocate the bath to an area of more constant ambient temperature.
-
4. Completely immerse the sensors to be verified into the bath with the certified or traceable sensor. Be sure the temperature of the water bath is equilibrated and stable. There should be no positive or negative trends in temperature readings taken from the water bath with the certified or traceable sensor.
-
5. Position the sensors next to each other as close as possible (without contacting each other). Stir or circulate the water bath and allow at least 2 minutes for the temperature to stabilize.
-
6. Without removing the sensors from the water bath, record the sensor measurements to the nearest 0.01°C or the maximum resolution of the displays.
-
7. Record three measurements at least 1 minute apart from each other within a 5-minute span for each sensor.
-
8. Calculate the mean of the three temperature measurements for each tested sensor then compare the mean value to the certified or traceable sensor.
-
9. Document the sensors' accuracy with difference in reference to the certified or traceable sensor in the calibration and maintenance logbook or electronic log. Entry should include the verification date, the accuracy of the sensor, and the certifier's initials.
3.2.3.2. Room Temperature or Above Calibration Verification
For a “room temperature” verification (about 20–25°C), the goal is to set up and maintain a bath of uniform ambient temperature. This procedure is recommended to be performed indoors, in a climate controlled or temperature stable area. An insulated container such as a cooler can be used with or without a circulator.
-
1. Fill a container of suitable size for the sensor verification about three-quarters full with water. An insulated container such as a Dewar flask or cooler is recommended. The verification container filled with water can be packed inside an outer container or box with insulation. Place the verification container in a climate-controlled room away from drafts, vents, windows, doors, and harsh lights.
-
2. Completely immerse the certified or traceable sensor in the water. Make sure that the temperature is uniform by stirring and checking at several locations within the bath with the certified or traceable sensor. The temperature should be constant. No positive or negative trends in temperature change should be detected within several minutes of equilibration. Depending on the starting temperature of the water, it may take several hours for the water in the container to equilibrate to ambient temperature.
-
3. Immerse the sensors to be verified into the water with the certified or traceable sensor.
-
4. Position the sensors next to each other as close as possible (without contacting each other). Stir or circulate the water bath and allow at least 2 minutes for the temperature to stabilize.
-
5. Without removing the sensors from the water bath, record the sensor measurements to the nearest 0.01°C or the maximum resolution of the displays.
-
6. Record three measurements at least 1 minute apart from each other within a 5-minute span for each sensor.
-
7. Calculate the mean of the three temperature measurements for each tested sensor then compare the mean value to the certified or traceable sensor.
-
8. Document the sensors' accuracy with difference in reference to the certified or traceable sensor in the calibration and maintenance logbook or electronic log. Entry should include the verification date, the accuracy of the sensor, and the certifier's initials.
For verification points greater than room temperature (about 20–25°C), use the same procedure as for the room temperature bath. If the verification container is small enough, it can be placed on a hot plate set on low and stirred with a magnetic stir bar. If the container is larger, a heater circulator can be used in the container to provide a water bath of constant suitable temperature. Heater circulators are available from scientific equipment suppliers and can usually be clamped to the side of a container to make a water bath.
3.3. In Situ Calibration Verification of Sensors
These procedures are for calibration verification of temperature sensors when equipment is not removed from service. Calibration verification in this case takes place throughout the year and range of temperatures at the field site accomplished by comparison of the sensor to be verified against a certified or traceable sensor. Groundwater and surface water sites visited throughout the year spaced at quarterly intervals should capture the range of temperatures of the site. This approach may not be applicable for all sites, especially nonflowing sites. See section 3.1 Determination of Points for Sensor Calibration Verification and section 2.2 Establishing and Maintaining a Traceable Sensor.
3.3.1. Surface Water In Situ Calibration Verification
This procedure can be used to verify the calibration of a deployed surface water temperature sensor where the sensor is left at the field site and checked against a certified or traceable sensor during site visits.
-
1. Completely immerse the certified or traceable sensor and the field sensor and position the sensors next to each other as close as possible (without contacting each other). The sensors should be in a flowing section of the water body but not in direct sunlight, if possible.
-
2. Allow the sensors to equilibrate for at least 2 minutes. There should be no positive or negative trends in temperature readings taken with the certified or traceable sensor.
-
3. Without removing the sensors from the water, record the sensor measurements to the nearest 0.01°C or the maximum resolution of the displays.
-
4. Record three measurements at least 1 minute apart from each other within a 5-minute span for each sensor.
-
5. Calculate the mean of the three temperature measurements for the tested sensor then compare the mean value with the certified or traceable sensor.
-
6. Document the sensors' accuracy with difference in reference to the certified or traceable sensor in the calibration and maintenance logbook or electronic log. Entry should include the verification date, the accuracy of the sensor, and the certifier's initials.
3.3.2. Groundwater In Situ Calibration Verification
These procedures can be used to verify the calibration of deployed groundwater temperature sensors. The sensors are left at the field site and checked against a certified or traceable sensor during site visits. Removing equipment from a well (or other field service), can mix the well water column and may require recalibration for other parameters, such as groundwater level or water-quality parameters. These disadvantages often make in situ calibration of groundwater sensors more practical.
3.3.2.1. Pumping Groundwater Calibration Verification
For groundwater in situ calibration verification, a pumping method can be employed using an insulated bucket or other suitable container. The temperature sensor comparison to a certified or traceable sensor is made above land surface and allows immediate reinstallation of the verified sensor.
-
1. Place a 1-gallon bucket in a box packed with insulation. A cooler partially filled with water can be used for multiparameter instruments. Place the container in an area where the temperature is constant such as the shade or a ventilated vehicle.
-
2. Pump water from the well into the bucket. Immerse the certified or traceable sensor and the sensor to be verified next to each other as close as possible (without contacting each other). Continue to pump water until the temperature in the bucket stabilizes. Pump water in the bucket at a flowrate suitable to keep the temperature constant. The bucket will be overflowing with water during this procedure. Alternatively, if the site is a water-supply well, water can be supplied to the bucket by a hose from a spigot instead of a separate pump.
-
3. Allow the sensors to equilibrate for at least 2 minutes. Be sure the temperature of the water bath is equilibrated and stable. There should be no positive or negative trends in temperature readings taken from the water bath with the certified or traceable sensor.
-
4. Without removing the sensors from the bucket, record the sensor measurements to the nearest 0.01°C or the maximum resolution of the displays.
-
5. Record three measurements at least 1 minute apart from each other within a 5-minute span for each sensor.
-
6. Calculate the mean of the three temperature measurements for the tested sensor then compare the mean value with the certified or traceable sensor.
-
7. Document the sensors' accuracy with difference in reference to the certified or traceable sensor in the calibration and maintenance logbook or electronic log. Entry should include the verification date, the accuracy of the sensor, and the certifier's initials.
3.3.2.2. Downhole Groundwater Calibration Verification
For groundwater in situ calibration verification, a downhole method can be employed. This procedure involves lowering a certified or traceable sensor to the same level as the deployed sensor to be verified. This procedure causes minimal disruption to the well water column and data collection activities.
-
1. Lower a portable and waterproof certified or traceable sensor to the exact depth of the sensor to be verified, such as a pressure transducer. For a pressure transducer used to measure depth-of-water, the depth of the pressure sensor below the measuring point is the offset used to calibrate the water level. The difference in depth between the temperature sensor and pressure sensor on the pressure transducer must be considered. This distance is often not available and should be determined and documented before the initial deployment.
-
2. Wait until the temperature measurements change less than 0.2°C every 5 minutes in both the certified or traceable sensor and the sensor to be verified. Be sure the temperature is equilibrated and stable. There should be no positive or negative trends in temperature readings taken with the certified or traceable sensor.
-
3. Without moving the sensors, record the sensor measurements to the nearest 0.01°C or the maximum resolution of the displays.
-
4. Record three measurements at least 1 minute apart from each other within a 5-minute span for each sensor.
-
5. Calculate the mean of the three temperature measurements for the tested sensor then compare the mean value with the certified or traceable sensor.
-
6. Document the sensors' accuracy with difference in reference to the certified or traceable sensor in the calibration and maintenance logbook or electronic log. Entry should include the verification date, the accuracy of the sensor, and the certifier's initials.
4.0. Measurement
Air and water temperature should be measured and recorded whenever water-quality samples are collected. Water temperature must always be measured in situ or in a well-designed groundwater flow-through cell and in a manner that ensures that the measurement accurately represents the intended sample conditions. Procedures in this chapter for measuring air and water temperature are for attended, discrete measurements. Sensors classified as certified, traceable, or verified may be used so long as the accuracy and precision requirements of the project are met and the sensor comparisons and verifications described in sections 2.1 Definitions, 2.2 Establishing and Maintaining a Traceable Sensor, and 3.0 Calibration Verification of Temperature Sensors are met.
4.1. Air
Sensors used to measure water temperature may not be well suited to measurement in air. Equilibration time for a sensor in air is longer than it is in water. Equipment, including multiparameter instruments, with embedded sensors suitable for measurement and deployment in water may require long equilibration times in air. Measure the air temperature as close as possible to the time when the temperature of the water sample is measured. Measure air temperature using a dry, verified temperature sensor.
-
1. Place or hang the sensor about 5 feet above the ground in a shaded area that is protected from strong winds but open to air circulation. In addition to avoiding direct sunlight, avoid areas of possible radiant heat effects, such as metal walls, rock exposures, or sides of vehicles.
-
2. Allow 3–5 minutes for the sensor to equilibrate, then record the temperature and time of day.
-
3. Report routine air temperature measurements to the nearest 0.1°C.
4.2. Water
4.2.1. Surface Water
The reported surface-water temperature must be measured in situ—do not measure temperature on subsamples from a sample compositing device. Measure temperature in such a manner that the mean or median temperature at the time of observation is represented (consult NFM 6.0, fig. 6.0–1). Record any deviation from this convention in the database and report it with the published data.
-
➢ Making a cross-sectional temperature profile first, to determine the temperature variability of the stream section, is recommended. A hand-held digital thermometer or multiparameter instrument works best for this purpose.
-
➢ To determine which sampling method to use, examine the cross-sectional profile and consider study objectives (see NFM 6.0).
-
➢ Measure temperature in those sections of the stream that represent most of the water flowing in a reach. Do not make temperature measurements in or directly below stream sections with turbulent flow or from the stream bank (unless this specifically represents the intended condition to be measured).
-
1. Use a sensor that has been verified within the past 12 months using the procedure outlined in section 3.0 Calibration Verification.
-
2. Record on field forms or electronic records the temperature variation from the cross-sectional profile, and the sampling method selected.
-
• Flowing, shallow stream.—Wade to the location(s) where temperature is to be measured. To prevent erroneous readings caused by direct solar radiation, stand so that a shadow is cast on the site for temperature measurement.
-
• Stream too deep or swift to wade.—Measure temperature by lowering the sensor from a bridge, cableway, or boat. Standalone temperature sensors are typically light weight and may need to be attached to a weighted cable. Do not attach a weight directly onto the sensor or sensor cable.
-
• Still-water conditions.—Measure temperature at multiple depths at several points in the cross section according to project objectives for the site.
-
-
3. Immerse the sensor in the water to the correct depth and hold for no less than 60 seconds, or according to the manufacturer’s guidelines, until the sensor equilibrates thermally. The sensor must be immersed properly while measuring the temperature; this might require attaching the sensor to a weighted cable.
-
4. Record the temperature reading of the display—do not remove the sensor from the water. When using a digital thermometer or multiparameter instrument, wait until the readings stabilize to within 0.2°C, then record the median of approximately the last five values. Record the readings to the maximum resolution of the display.
-
5. Remove the temperature sensor from the water, rinse it thoroughly with deionized water, blot it dry, and store it. See section 2.3 Maintenance, Cleaning, and Storage for more details.
-
6. Record the stream temperature on field forms or electronic records. Determine the values as follows (see NFM A6.0, fig. 6.0-1):
4.2.2. Groundwater
Measurements of groundwater temperature must be made downhole or with a flowthrough system at the end of purging to ensure that the temperature measured accurately represents ambient aquifer water conditions (consult NFM A6.0 for guidance). Do not report a temperature value measured from a bailed groundwater sample. Select either the downhole or flowthrough-chamber sampling system (see NFM 6.0, fig. 6.0–6) and record the method used.
-
1. Use a sensor that has been verified within the past 12 months using the procedure outlined in section 3.0 Calibration Verification.
-
2. Prepare the instruments for either the downhole or the flowthrough-chamber system.
-
• Downhole system.—Lower the sensor in the well to just below the pump intake (the intake location depends on the sampling objectives).
-
• Flowthrough-chamber system.—Install the sensor in the chamber so it is immersed according to manufacturer’s instructions. The pump tubing from the well to the chamber should be as short as possible, out of direct sunlight, insulated, and off the ground. Keep the chamber out of direct sunlight and excessive wind.
-
-
3. Begin water withdrawal from the well. Allow the temperature sensor to equilibrate with groundwater temperature for no less than 60 seconds or in accordance with the manufacturer’s guidelines; record the readings and time intervals throughout the period of purging.
-
4. Toward the end of purging, record five or more sequential measurements, spaced at increments of 3 to 5 minutes or more. Record the readings to the maximum resolution of the display.
-
• If the temperature is stable within the 0.2°C criterion, report the median of the final five measurements to the nearest 0.1°C (see NFM 6.0, table 6.0–1).
-
• If the stability criterion has not been met, extend the purge time and consult the well-purging objectives of the study. Report the median of the last five (or more) sequential measurements and record any instability on field forms.
-
5. Remove the temperature sensor from the water, rinse it thoroughly with deionized water, blot it dry, and store it. See section 2.3 Maintenance, Cleaning, and Storage for more details.
-
5.0. Troubleshooting
Contact the equipment manufacturer if the suggestions on table 6.1-1 fail to resolve the problem, or if additional information is needed. There are very few problems with temperature sensors and digital thermometers that can be solved in a field setting. The best practice is to have new, verified water temperature sensors available to replace malfunctioning field sensors. Be sure to follow manufacturer’s recommendations for cleaning and troubleshooting in general.
6.0. Reporting
USGS temperature measurements should be stored in the National Water Information System (NWIS) database (U.S. Geological Survey, undated). These data may be published as the verified negative or positive value measured.
At the time of writing (2024), NWIS (Aquarius Time Series and Aquarius Samples) is undergoing system changes that should allow the data to be stored with its associated uncertainty. When NWIS can store uncertainty, it is to be stored with the data in the form of metadata (like ±0.2°C) or the manufacturer’s stated accuracy that is verified through the procedures in section 3.0 Calibration Verification. Until NWIS can store the uncertainty of the data, only data that are verified as accurate to less than or equal to ±0.2°C should be stored in NWIS. Data not verified as accurate to less than or equal to ±0.2°C should be published as a USGS data release with its associated verified uncertainty. Temperature data may be stored in the database unrounded. Unrounded temperature data in the database will be rounded when retrieved for publication.
Acknowledgments
The information in the U.S. Geological Survey (USGS) National Field Manual (NFM) is based on existing manuals, various reference documents, and a broad spectrum of expertise provided by USGS colleagues. Authors of previous versions of NFM chapter A6.1 were M.E. Brigham, E.A. Ciganovich, I.M. Collies, J.V. Davis, C.M. Eberle, R.J. Hoffman, R.T. Iwatsubo, J.K. Kurklin, R.J. LaCamera, V.W. Norman, C.E. Oberst, B.B. Palcsak, K.A. Pearsall, D.B. Radtke, F.C. Wells, and F.D. Wilde. The persistence and spirit that all of our colleagues brought to the development of a national field manual were invaluable.
The following USGS colleagues provided content and detailed reviews that improved the technical quality of this report: Gerolamo Casile, Stanley Skrobialowski, Timothy Oden, Lee Bodkin, Amanda Booth, Allison Casile, Joel Galloway, Karl Haase, Brittney Izbicki, Kevin Kotun, Craig Mobley, Diana Phillips, Patrick Rasmussen, Kimberly Shaffer, and Evan Tillman. Editorial and production assistance from Mary Heinz and Cathy Knutson is greatly appreciated. These individuals contributed to the accuracy, quality, and usability of the NFM, and demonstrated much patience as we traversed the difficult task of implementing the new format.
Special thanks are extended to Franceska Wilde (USGS, retired), who led the effort for the NFM from its inception until her retirement in 2014; the USGS NFM Steering Committee (Gerolamo Casile, Alissa Coes, Michael Manning, Timothy Oden, Lisa Olsen, and Stanley Skrobialowski); Cherie Miller (USGS, retired), who led the effort from 2016 to 2018; and Gerolamo Casile, who assumed responsibility for the NFM in 2018.
Selected References
ASTM International, 1996-2024, Temperature Standards, in ASTM Book of Standards, ASTM International, accessed July 12, 2024, at https://www.astm.org/products-services/standards-and-publications/standards/temperature-measurement-standards.html.
Eaton, A.D., Clesceri, L.S., Rice, E.W., and Greenberg, A.E., 2005, Laboratory and field methods, sec. B of part 2550 in Standard methods for the examination of water and wastewater (21st ed.): Washington, D.C., American Public Health Association, American Water Works Association, and Water Environment Federation, p. 2-61—6-62.
Hem, J.D., 1989, Study and interpretation of the chemical characteristics of natural water: U.S. Geological Survey Water-Supply Paper 2254. (3rd ed.), p. 18. Accessed July 12, 2024 at https://pubs.usgs.gov/wsp/wsp2254/pdf/section2.pdf.
ICL Calibration Laboratories, Inc., 2024, ICL Calibration Laboratories, Inc.: FAQs and Help Topics, ICL Calibration Laboratories, Inc., website, accessed July 12, 2024, at https://icllabs.com/faqs-and-help-topics/.
NIST, 2023, Definition of Traceability: NIST webpage, accessed January 25, 2024, at https://www.nist.gov/metrology/metrological-traceability.
NIST, 2024, National Voluntary Laboratory Accreditation Program: NIST webpage, accessed October 10, 2024, at https://www.nist.gov/nvlap.
Ripple, D.C., and Strause, G.F., 2005, Selection of alternatives to liquid-in-glass thermometers (reprinted 2005): Journal of ASTM International, v. 2, article JAI13404, 10 p. accessed January 8, 2024, at https://tsapps.nist.gov/publication/get_pdf.cfm?pub_id=830919.
Stevens, H.H., Jr., Ficke, J.F., and Smoot, G.F., 1975, Water temperature—influential factors, field measurement, and data presentation: U.S. Geological Survey Techniques of Water-Resources Investigations, book 1, chap. D1, 65 p. Accessed July 12, 2024, at https://pubs.usgs.gov/twri/twri1-d1/html/pdf.html.
U.S. Geological Survey, 2002, Water-quality field methods/ National Field Manual for the Collection of Water Quality Data: U.S. Geological Survey Office of Water Quality Technical Memorandum 2002.13, accessed October 10, 2024, at https://water.usgs.gov/water-resources/memos/memo.php?id=2228.
U.S. Geological Survey, 2016, Guidance for the collection and disposition of USGS water-quality-data records—Specifically addressing electronic records for field notebooks and calibration notebooks: U.S. Geological Survey Office of Water Quality Technical Memorandum 2016.09, accessed October 10, 2024, at https://water.usgs.gov/water-resources/memos/memo.php?id=2058.
U.S. Geological Survey, [undated], USGS water data for the Nation: U.S. Geological Survey National Water Information System database, accessed October 10, 2024, at https://doi.org/10.5066/F7P55KJN
U.S. Geological Survey, [variously dated], National field manual for the collection of water-quality data: U.S. Geological Survey Techniques of Water-Resources Investigations, book 9, chaps. A1–A9, available online at https://pubs.water.usgs.gov/twri9A.
Wagner, R.J., Boulger, R.W., Jr., Oblinger, C.J., and Smith, B.A., 2006, Guidelines and standard procedures for continuous water-quality monitors—station operation, record computation, and data reporting: U.S. Geological Survey Techniques and Methods, book 1, chap. D3. available online at https://pubs.usgs.gov/tm/2006/tm1D3/.
Wood, W.W., 1976, Guidelines for collection and field analysis of ground-water samples for selected unstable constituents: U.S. Geological Survey Techniques of Water-Resources Investigations, book 1, chap. D2, 24 p. available online at https://pubs.usgs.gov/twri/twri1-d2/.
Conversion Factors
Abbreviations
cm
centimeter
DIW
deionized water
EDI
equal-discharge increment, isokinetic sampling method
EWI
equal-width increment, isokinetic sampling method
FLIR
forward-looking infrared
IR
infrared
L
liter
µS/cm
microsiemens per centimeter
NFM
U.S. Geological Survey National Field Manual for the Collection of Water-Quality Data
NIST
National Institute of Standards and Technology
NWIS
U.S. Geological Survey National Water Information System
QA
quality assurance
USGS
U.S. Geological Survey
WMA
U.S. Geological Survey Water Mission Area
Disclaimers
Any use of trade, firm, or product names is for descriptive purposes only and does not imply endorsement by the U.S. Government.
Although this information product, for the most part, is in the public domain, it also may contain copyrighted materials as noted in the text. Permission to reproduce copyrighted items must be secured from the copyright owner.
Suggested Citation
U.S. Geological Survey, 2024, Temperature: U.S. Geological Survey Techniques and Methods, book 9, chap. A6.1, 14 p., https://doi.org/10.3133/tm9A6.1. [Supersedes USGS Techniques of Water-Resources Investigations, book 9, chap. A6.1, version 2.0.]
ISSN: 2328-7055 (online)
Publication type | Report |
---|---|
Publication Subtype | USGS Numbered Series |
Title | Temperature |
Series title | Techniques and Methods |
Series number | 9-A6.1 |
DOI | 10.3133/tm9A6.1 |
Year Published | 2024 |
Language | English |
Publisher | U.S. Geological Survey |
Publisher location | Reston, VA |
Contributing office(s) | WMA - Observing Systems Division |
Description | v, 14 p. |
Online Only (Y/N) | Y |
Additional Online Files (Y/N) | N |